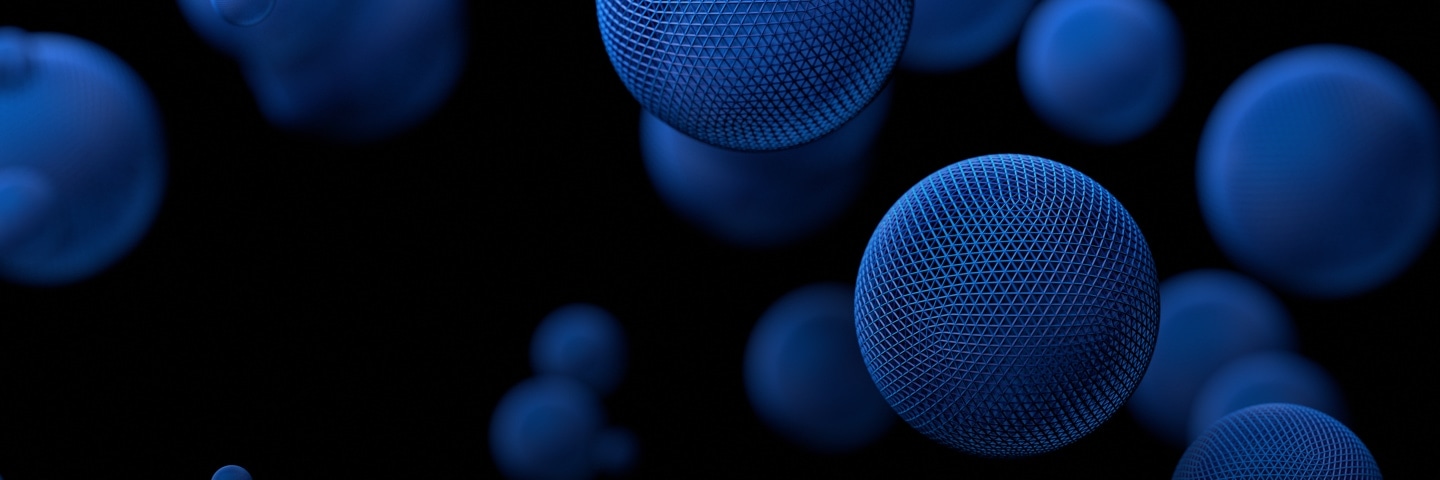
Case Study
Press Fitting Seals for Gas Application
A Press Fitting Seal for Water Applications is Transformed into a Robust Gas Press Fitting Design
Challenge
Design a rubber seal for gas press fittings that’ll last 50 years and comply with stringent global regulations.
A long-standing Minnesota Rubber & Plastics customer wanted to extend its current press fittings products with a new line for the gas market. We had previously designed a press fitting seal that provided a resistance force during assembly, which gives the plumber tactile feedback during the insertion process. This friction restricts the fitting from coming apart prior to pressing [Figure 1].
The customer now wanted these same features on a new line of natural gas and liquid petroleum gas fittings, which called for a new compound formulation. These new features make it easier to detect leaks and help techs properly check all system fittings. The unique design automatically rotates the seal for the plumber to prevent the sealing surface from coming into contact with the seal parting line.
The challenge was formulating a new compound in our advanced materials lab to resist chemical and physical degradation caused by a wide range of fuels and gases.
Solution
A custom HNBR formulation that withstands high pressures and temperatures.
To develop and select the perfect compound for this application, Minnesota Rubber & Plastic’s advanced materials lab researched the regulatory requirements and material performance targets. Based on these findings, we chose HNBR as the base compound.
During step two, we optimized the HNBR compound to withstand the client’s rigorous compression set resistance requirement, as well as heat and chemical resistance. Additionally, to meet the customer’s color requirement, we produced the
compound in yellow, which signals to plumbers and inspectors that the correct fittings were installed.
With rubber seals manufactured using the new compound, compression set was tested and exposed at temperatures of 100°C and 150°C, and produced lower compression set test results than competitors. These higher values resulted in:
• Longer sealing force retention
• Longer seal life
• Enhanced safety
What’s more, at low temperatures, the elastic modulus maintained its flexibility and sealing performance.
Results
A “bullet-proof” seal helped make a press-to-connect fitting the best on the market.
Extensive customer and regulatory agency testing took place to certify the fittings and HNBR seals, which helped our customer go to market with a more cost-effective and competitive offering.
Passed regulatory tests included CSA LC4, (1000°C sealing) and DIN EN 549. Based on client feedback, our customer’s new product’s ultimate success is due to close collaboration between both companies, an innovative fitting design, and a robust seal that will last a half-century.

Physical properties | MRP’s C2536YH | HNBR Competitor |
Micro-Hardness Type M, IRHD | 64.4 | 70.1 |
Compression Set Resistance, 22 hours @ 100°C, % | 11.2 | 21.4 |
Compression Set Resistance, 22 hours @ 150°C, % | 18.4 | 60.6 |
Elastic Modulus at 0°C (MPa)* | 13.4 | 18.3 |
Elastic Modulus at -20°C (MPa)* | 24.8 | 60.8 |
Elastic Modulus at -30°C (MPa)* | 100.4 | 264.5 |
Tg per DMA (°C)* | -40.4 | -34.9 |
Color | Yellow | Yellow |
Print-Ready Case Study
Download this case study in PDF format.
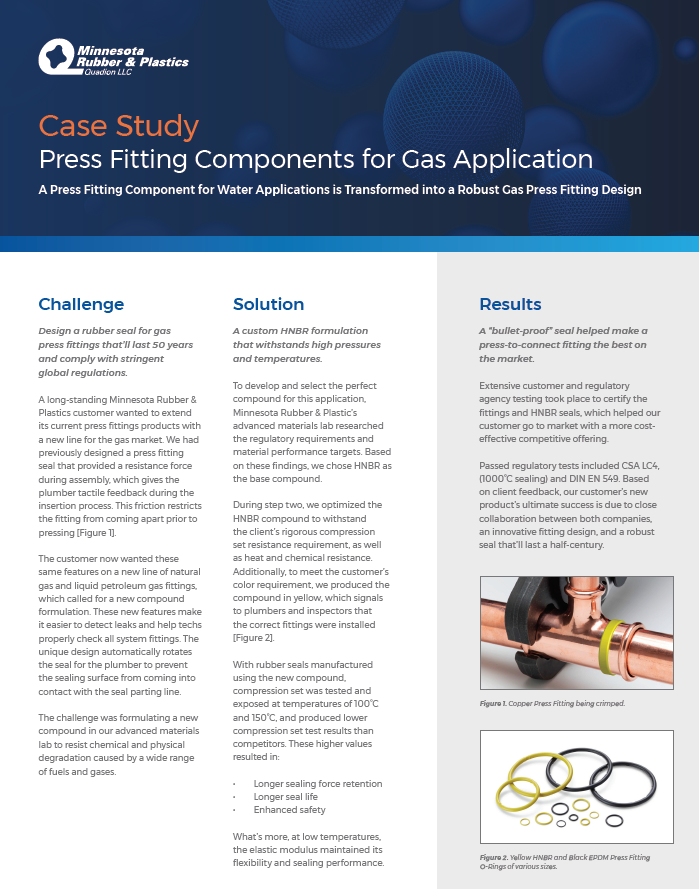