A Superior Component Design &
Prototyping Experience
Get to market faster. Make meaningful cost reductions. Or create a differentiated product that outperforms everyone’s expectations in the field. We can help you achieve those kinds of outcomes with integrated component design and prototyping services.
Integrated Services
Connected design, prototyping and manufacturing drives superior outcomes for your products and ensures components are designed for manufacturability at scale.
Unmatched Expertise
Engage us early in the design process, and together, we’ll reduce rework and build a superior component or assembly and allow you to deliver the best end results.
Production Intent Prototyping
We can quickly fabricate a production-intent part or assembly, and scale quality production once you’re ready to bring the product to market.
Innovative NPD Process
Our 7-step process delivers optimal product designs, while lowering costs and improving speed to market.
Smarter Manufacturing
Our advanced Mold Flow Analysis (MFA) and Finite Element Analysis (FEA) simulations ensure quality in production and performance in real-world conditions.
Experience It All
Engage with our new Innovation Center virtually or in-person to collaborate with our experts and participate in the entire design and prototype process under one roof.
Hear from our experts: How is a prototype built?
Leverage Our Vast Design Expertise
Finding the ideal design, including geometry and material characteristics, presents hidden complexities. To ensure optimal performance in the field and to guarantee the best form, fit and function, seals must be designed with every end-use requirement in mind. Discover how we can make any component application — work better for you.
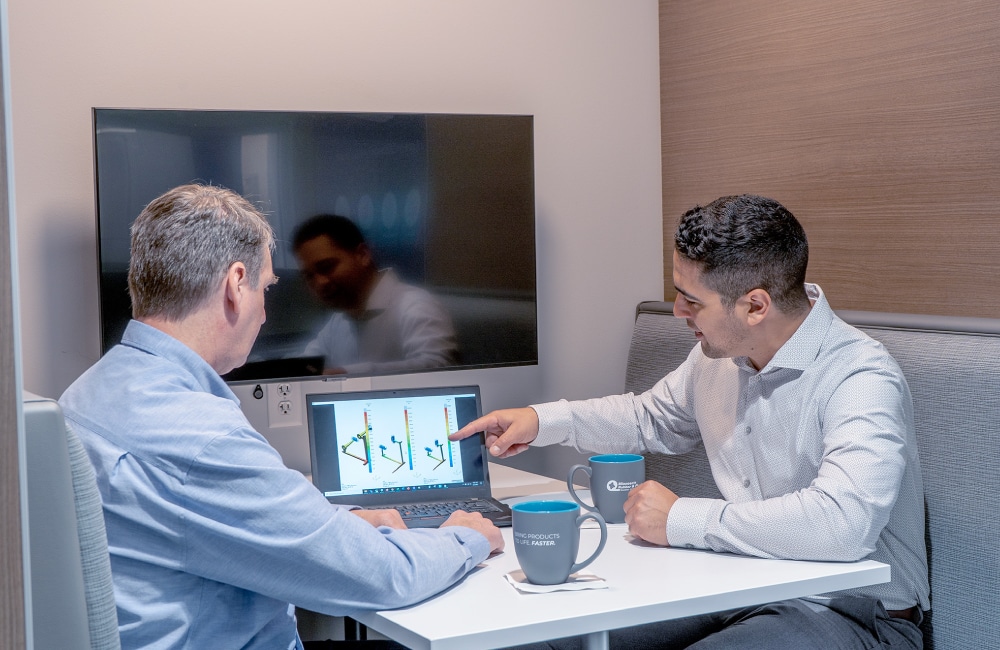
How We Ensure Manufacturability
Our advanced mold flow analysis (MFA) processes allow us to control how materials flow and cure, so we can create the perfect geometries for your parts. We use advanced analytic software — optimized for both elastomers and thermoplastics — to ensure quality, speed and efficiency in the manufacturing process. Our multi-factor analysis software – Finite Element Analysis (FEA) – predicts how a set component reacts to real-world forces including vibration, heat, fluid flow, and other physical effects.
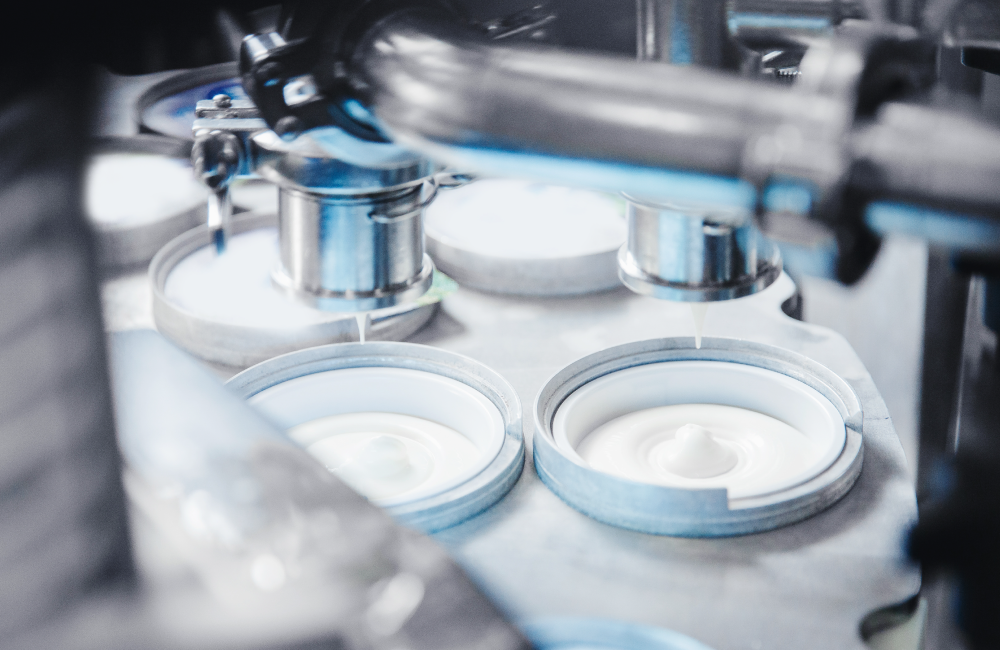
Production-Intent Prototype Development Fast
Moving forward with a component design that can’t be manufactured effectively is like driving the wrong direction for hours on a family vacation. Returning to the starting point is painful and there’s no way to recover the lost time.
Our prototyping services keep you from wasting time heading in the wrong direction, and bypasses the typical delays with production intent prototypes. We can quickly fabricate a scale model of your part or assembly, then use those models to test the design and create the optimal materials, tooling, and process to produce the component at scale.
While additive manufacturing is a great tool for some applications, it simply can’t replace production-intent prototypes in critical-to-function applications. Our approach ensures that the parts we develop with your team are intended for a production environment. This brings predictability and repeatability to the manufacturing process.
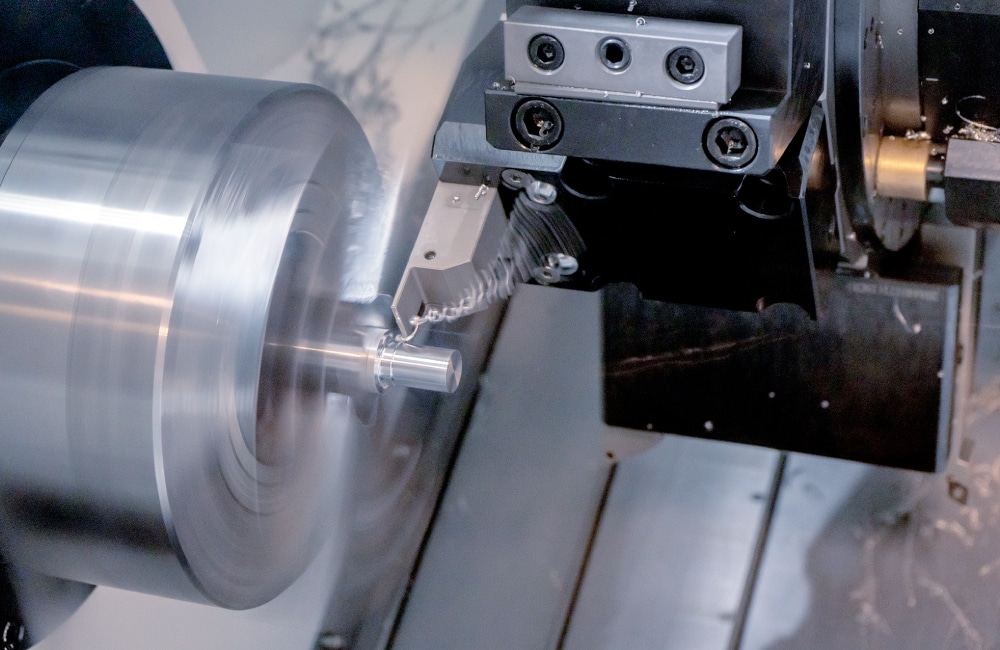
In-house Tooling Engineers Ensure Manufacturing Success
Our integrated design-prototype-test-build process is staffed by a dedicated team of experienced tooling engineers. This team supports our manufacturing operations for rubber, silicone, LSR and thermoplastic components. In-house tooling expertise and equipment allows us to iterate faster and improve speed time to market. This also includes careful planning and monitoring for key considerations in the manufacturing process, such as compression, transfer, insert over molding and injection molding.
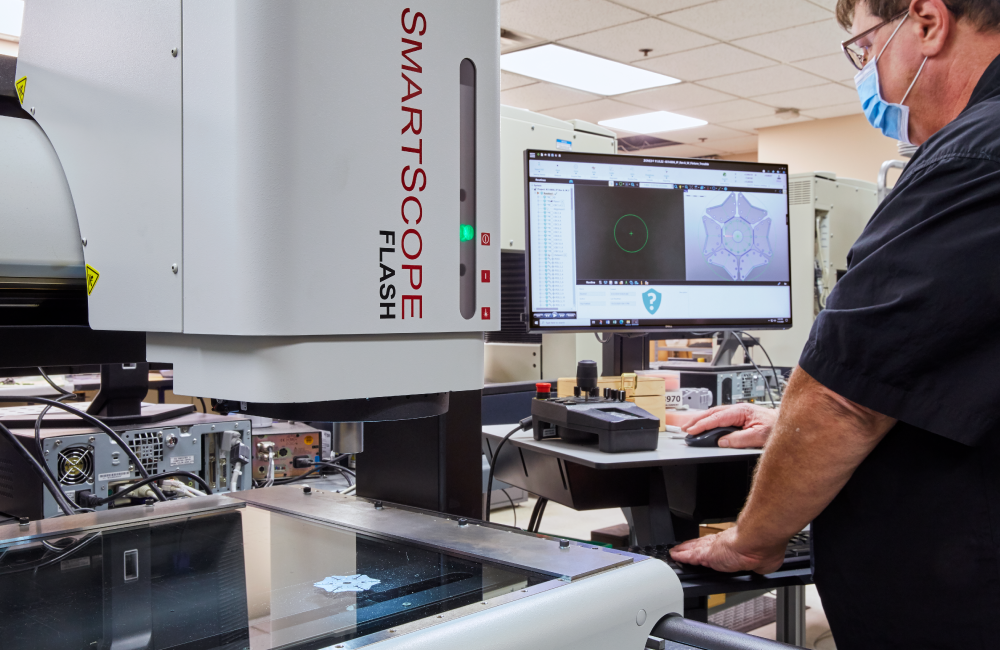
Commitment to Quality and Industry Standards
Our strict adherence to quality protocols and systems underpins our integrated process. Our commitment to quality ensures compliance with the specific regulatory standards of the industries you serve.
Get Quality Products to Market Faster
We understand you’re under pressure to launch products quickly without compromising on cost control or quality.
We can help. Send us an inquiry and one of our experts will respond promptly.