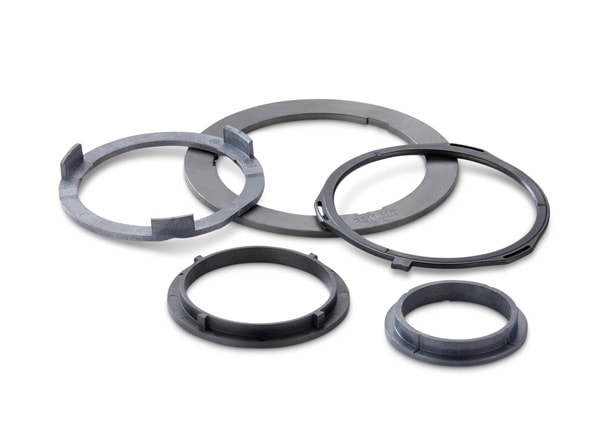
Assemblies
When a designer specifies rubber or plastic for a product or component, it’s because no other material can duplicate the required performance characteristics. However, most design engineers do not have the time to become rubber and plastic experts.
Our experience in applications for high-performance materials and thermoplastic elastomers allows us to view a new design or re-design criteria, objectively. As the components we produce are typically part of a larger assembly, many customers have benefitted from our part consolidation recommendations that allow us to design, develop manufacture, test, package and ship their completed assembly.
In order to meet critical time-to-market requirements we provide creative solutions for assembly programs. Whether it is a simple two component sub-assembly or a complex, multi-component rubber and plastic assembly that incorporates inserts, and hotplate welding, we offer cost-effective engineered solutions.
What’s more, we know how to maintain the integrity of your basic design while taking into consideration factors such as shrink distortion and parting lines; this helps avoid surprises when it comes time to manufacture, assemble and use the end product.
As the relationship between materials, parts and end-use performance need to be addressed, we also know how to solve problems arising from torque values and sealing contacts. We then ensure that the rubber and plastic materials complement each other’s tolerance capabilities. Once the design is complete, we can follow through with testing through the use of tools, such as FEA, where benefits such as increased strength, reduced material use and reduced costs can be realized.