Case Studies
Learn more about the work we’ve done and how it can help your business.
Read Trelleborg Healthcare & Medical case studies here.
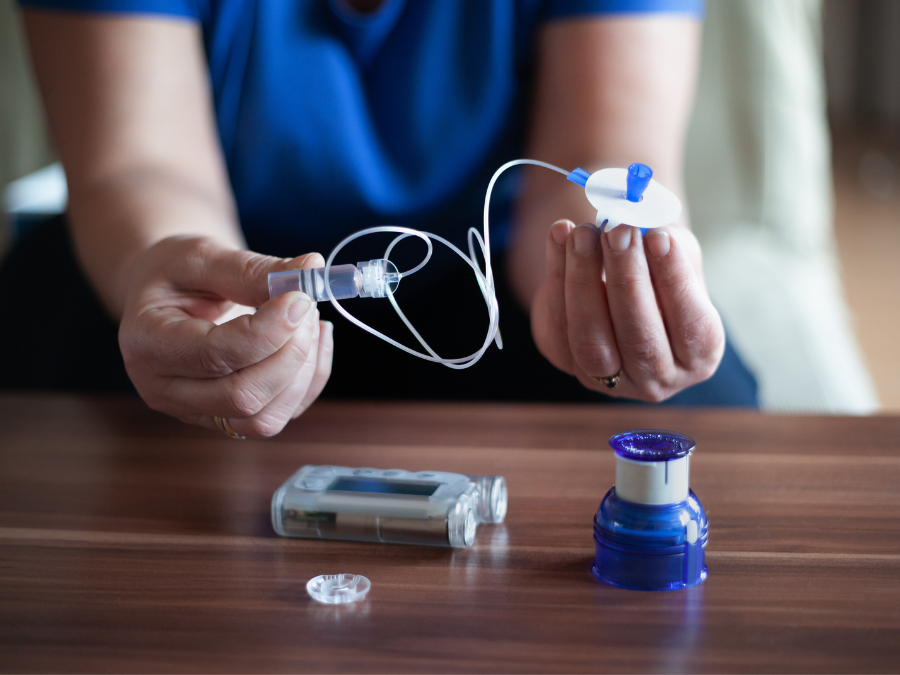
Tailoring Drug Delivery and Storage Systems to Meet the Evolving Market
The wearable industry continues to expand, driving demand for smaller device sizes of existing applications and developing new applications to deliver drug products. Solution providers with materials science as a key capability can lead the way with new material formulation offerings that push boundaries once considered impossible. Learn how.
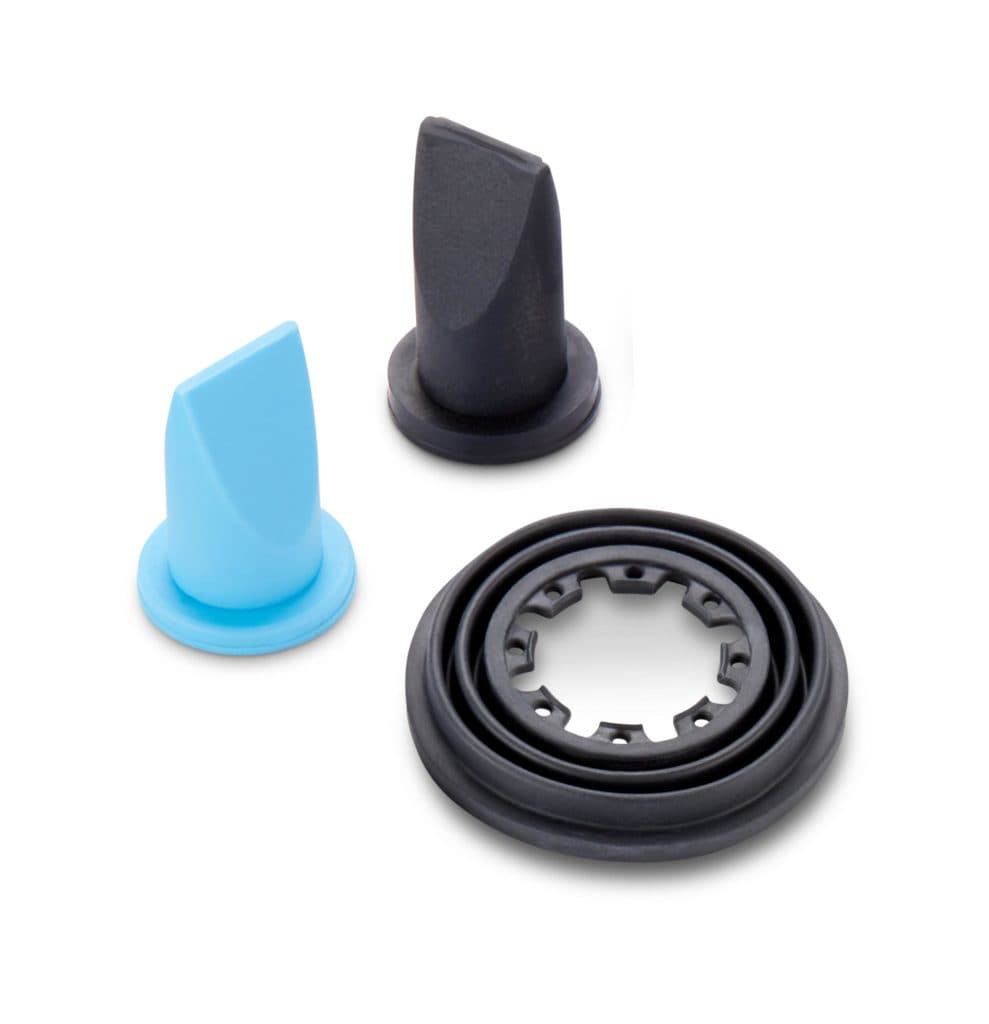
Developing a Custom Material for Trocar Seal Surgical Applications
The elastomer material for a customer’s new trocar surgical application was catching on material during insertion, often tearing the seal. They turned to our advanced materials group (AMG) team to create a material that solved this primary concern. See how our AMG team solved the problem and helped to make the trocar a superior solution for physicians.

New Material and Design for Rubber Umbrella and Bell Valves
Our client wanted us to create a custom rubber material for umbrella and bell valves leading to a more robust version of existing critical pump sealing components. At the same time, we would develop the material and manufacture the valves from our design facility in China, close to our client’s manufacturing operations. In response, we created better valve sealing performance; with elongation at break achieving 662%, a critical improvement.
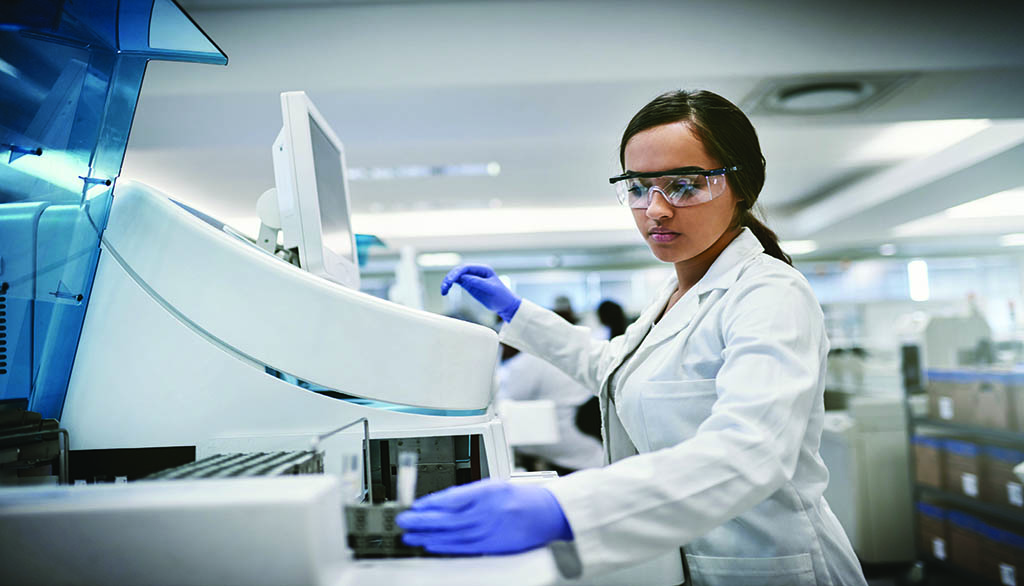
New Material Formulation Leads to Seal for Point-of-Care Diagnostics
Our team was part of the rapid response to urgent COVID-19 patient needs. We created a new material formulation for a point-of-care medical diagnostics seal that meets strict chemical and mechanical requirements.
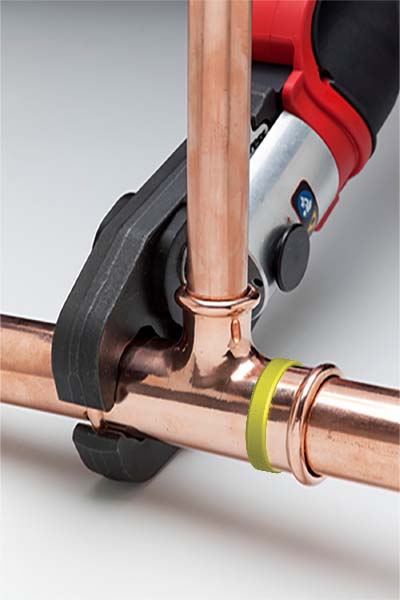
Press Fitting Components for Gas Application
We were challenged to design a rubber seal for gas press fittings that’ll last 50 years and comply with stringent global regulations. In response we created a custom HNBR formulation that withstands high pressures and temperatures. This resulted in a “bullet-proof” seal that helped make a press-to-connect fitting the best on the market.

Custom Formulated Material Delivers High Performance for a Surgical Seal Solution
A large medical technology company aimed to upgrade its medical device solution used primarily to cut and cauterize tissue in minimally invasive surgeries. The goal was to improve the design to allow surgeons to reuse the device by creating a disposable biocompatible flexible sleeve cover for the surgical instrument.
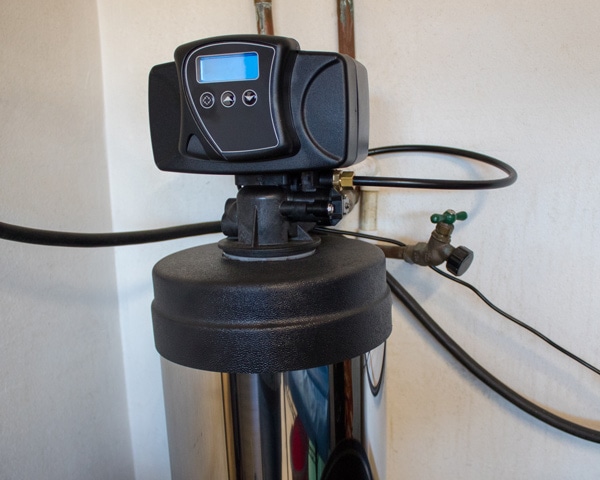
A More Durable Seal Reduces Warranty Claims for a Premium Water Softener Valve Manufacturer
A national manufacturer of premium water softener valves had been experiencing an increase in warranty claims from loyal owners. The company — a long-time Minnesota Rubber & Plastics customer — reached out to our engineering team to help them troubleshoot what was behind the warranty claims.
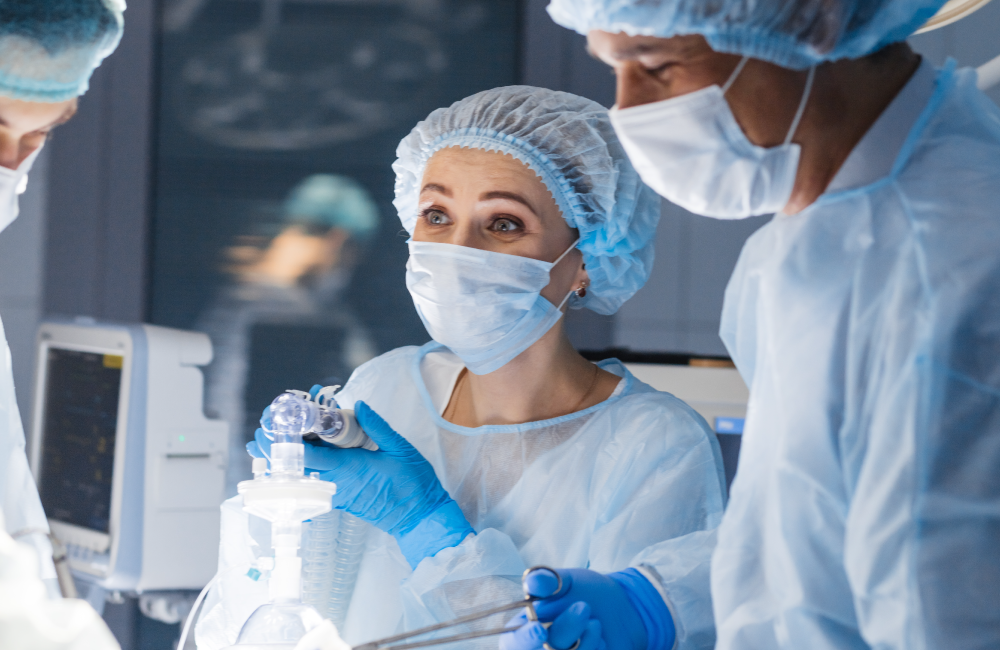
Wilson Wolf G-Rex® Gas Permeable Cell Culture Device Molded And Assembled By Minnesota Rubber And Plastics
Wilson Wolf created a paradigm shift with its cell culture design disrupting age-old beliefs regarding cell production. Minnesota Rubber and Plastics (MR&P) facilitated the unique design with an efficient, high quality molded, assembled and packaged G-Rex branded product ready for the medical marketplace.
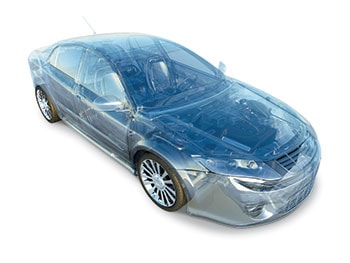
How Assembly Design And Manufacturing Improves Products
Engineered components, when combined into assemblies, can advance a product’s performance as they have in today’s highly efficient and reliable automobiles. New standards are set when individual components are redesigned into more efficient assemblies leading to vastly improved performance. Such is the case with vehicles of all types as most components such as shock absorbers redesigned of new, lighter materials last longer and are more cost effective to manufacture.
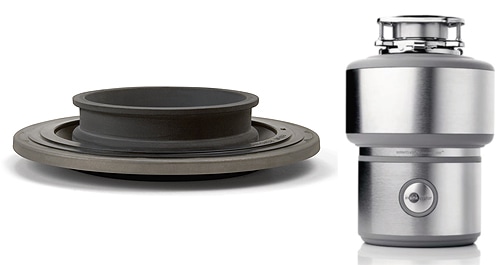
How Over-molding Improves Product Performance
Creating molded rubber parts with inserts involves considerable preparation before and after molding. These tips can help ensure a durable finished part while minimizing production costs.
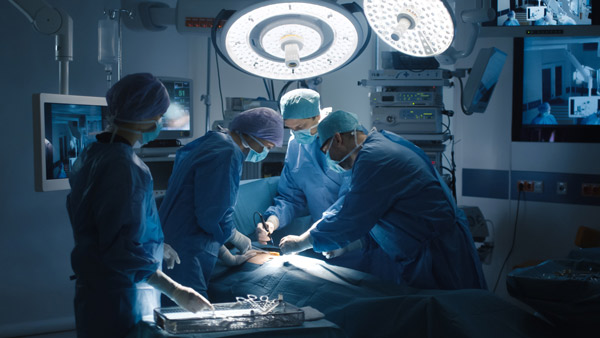
Medical Device Sealing Solutions
What Designers and Manufacturers Need To Know, Avoid And Consider When Planning Seals In A Device.
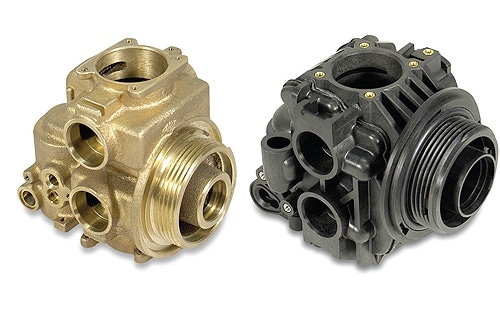
Tips for Designing Plastic Parts
When designing with plastic, the goal is to achieve a technically accurate design that functions well and can be cost effectively manufactured. Following these basic tips will help in accomplishing these goals and accelerate the designing process.