Global Manufacturing and Supply Chains
Local Presence, Global Reach
Resilient Supply Chains through Global Manufacturing
As manufacturers become increasingly global and establish manufacturing and development sites throughout the world, it is vital to partner with suppliers that also have a global manufacturing footprint. Diversified global manufacturers can effectively help you avoid supply chain disruptions, while also providing local support and customized solutions.
In the last decade, Minnesota Rubber & Plastics, now part of Trelleborg, has focused on expanding our global reach and broadening our R&D, materials development, and manufacturing and testing capabilities. The acquisition of MRP by Trelleborg ensures that the capability and technology demands of elastomer and thermoplastic component manufacturers worldwide are further supported by a highly experienced team of experts, a broad range of materials and manufacturing capabilities, and a robust, global supply chain.
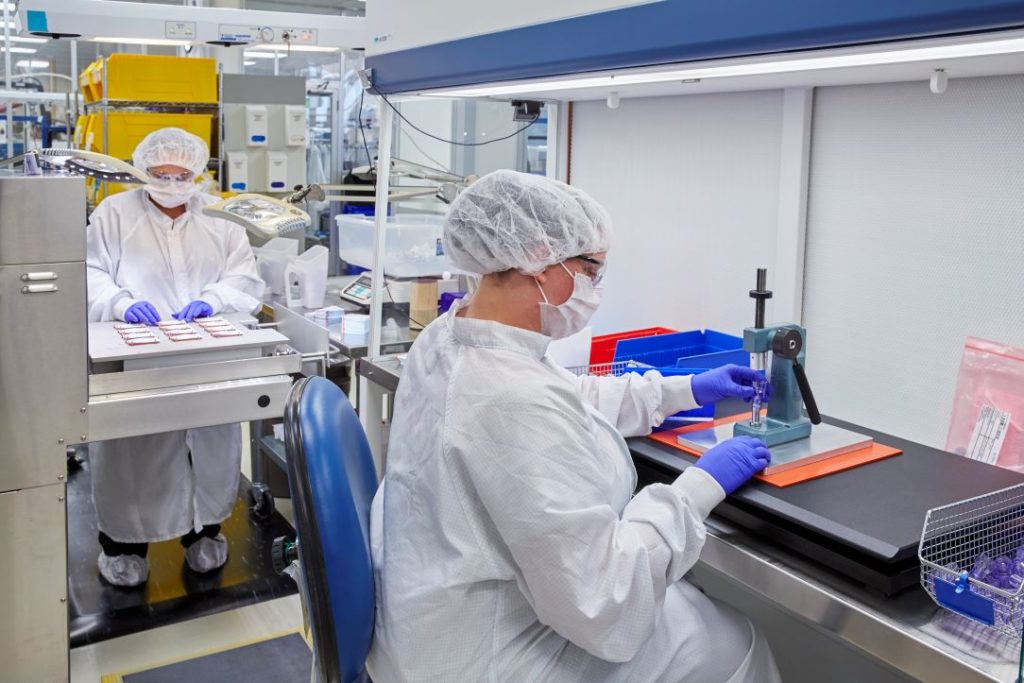
Our experts communicate with customers in their local languages so that, regardless of location, they have access to a variety of materials, such as Liquid Silicone Rubber (LSR), thermoplastics, black rubber, bioresorbables and other polymers and elastomers. Additionally, we serve customers globally with capabilities including silicone molding, extrusion, sheeting, dipping, and coating; overmolding; plastic injection molding; multicomponent manufacturing; drug-eluting technologies; engineered coated fabrics; and other technologies.
Our global manufacturing facilities operate under strict ISO guidelines, including ISO 13485, IATF 16949, and ISO 9000. Our facilities also operate under a corporate-wide Environmental Management System registered to the International Standards Organization ISO-14001.
Local manufacturing location decisions can be made per component, depending on part complexity, labor content, supply chain risk level, demand, and parts can be produced through efficient geographical supply chain consolidation. For example, some customers purchase the same rubber components in both the US and China. By producing the component in two locations, at both the China and US facilities, Trelleborg can provide customers better supply chain continuity.
Our Expanded Capabilities and Global Footprint as a Part of Trelleborg Include:
- 61 Customer Solutions Centers
- 41 Manufacturing Sites
- 10 R&D Centers
- 1 Customer Innovation Center
- 5 Logistics Centers
- 3 ServicePLUS Centers
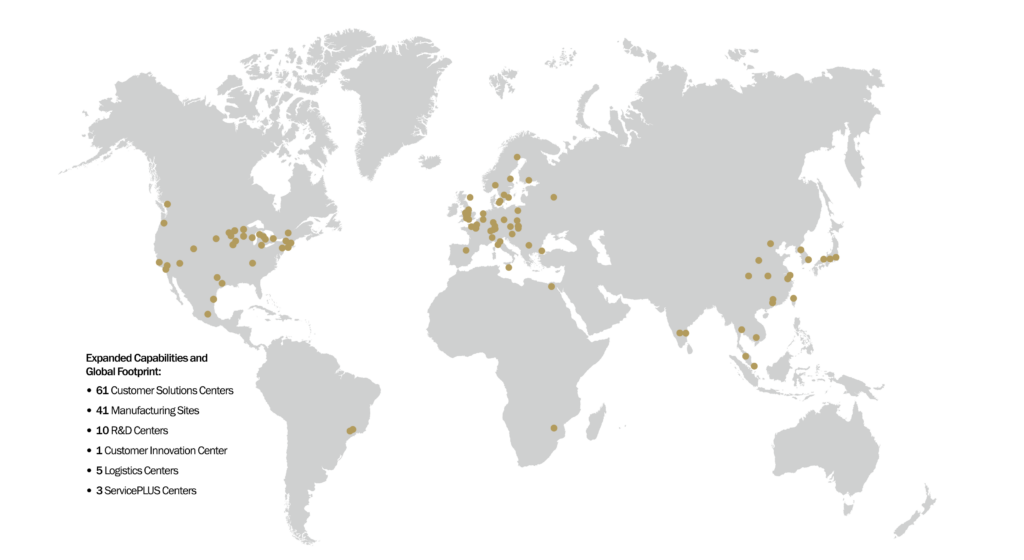