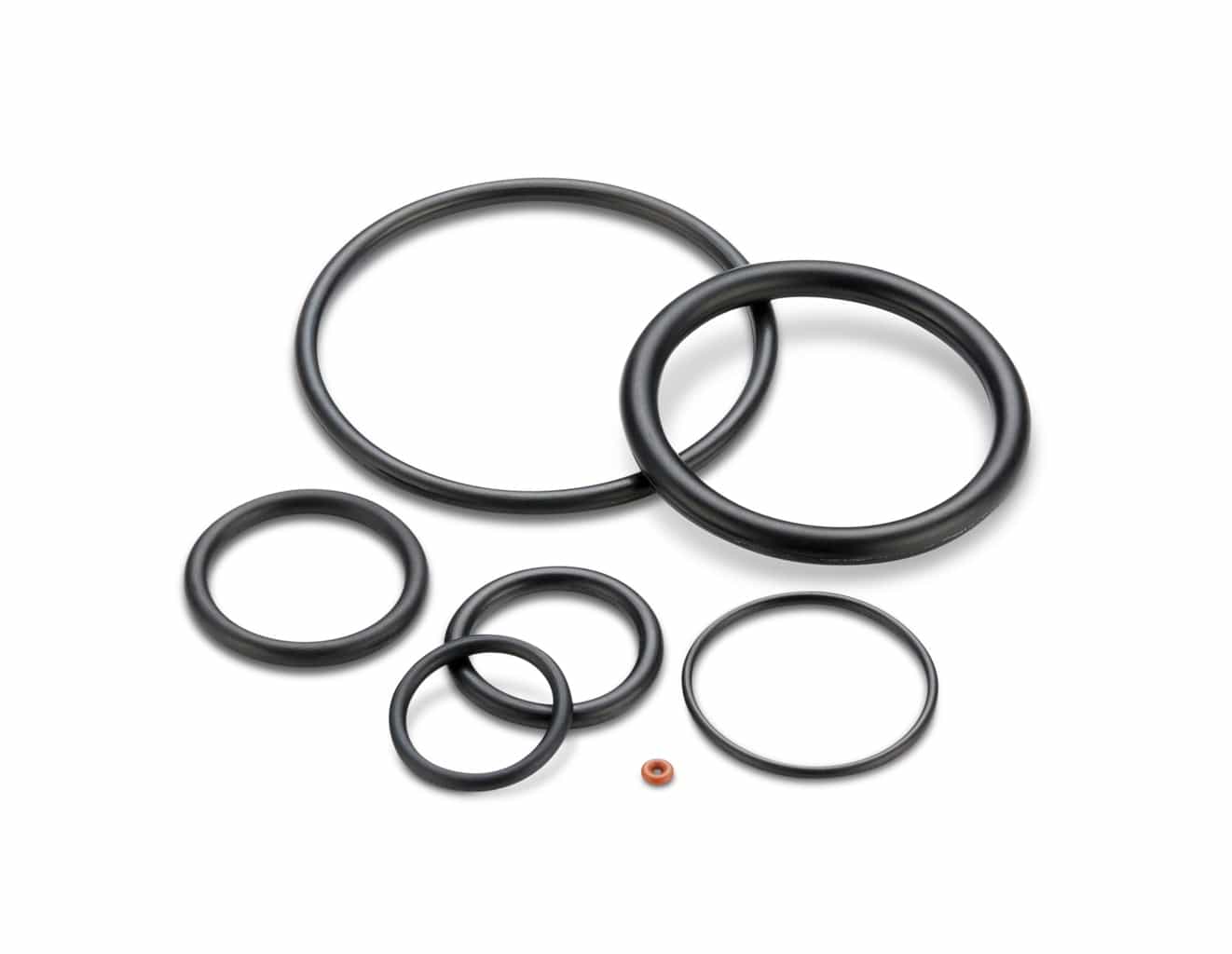
Compression Seals & Gaskets
The following is a listing of technical resources related to our custom compression seals, gaskets, tubing, and bumpers.
Profile Constructs

Dense
The majority of our extruded parts are manufactured using dense materials. Dense profiles are resilient and extrudable whereas some other constructs can only be molded. We offer a wide range of dense materials to select from, including TPV, EPDM, Neoprene, Silicone, and FKM.
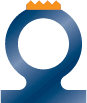
Co-Extruded
Some applications require two types of materials (usually having different durometers) to be joined together to form one part. A typical application involves a rigid component that acts as a retainer and a flexible component to act as a seal or bumper. This is most common with plastic materials.
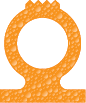
Sponge
Sponge extrusions provide a soft, supple seal while optimizing material usage. Sponge profiles should not be used where compression set is important, because the part will eventually take a permanent set. We do not have expertise with sponge extrusions and can recommend other suppliers if this is what you need.
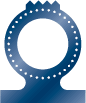
Fabric Reinforced
Fabric reinforcement serves many purposes. Embedded fabric can strengthen a part’s tensile strength which will allow it to withstand harsh applications. It also can be used on a part’s surface to reduce coefficient of friction. At Pawling EP, fabric reinforcement can only be applied by molding the part.

Multi Laminate
Multi-laminate designs are used in extreme applications, like airplane hatch seals. Aerospace applications use a multi-laminate construct of fabric, silicone, and polyester. The outer fabric reduces the part’s co-efficient of friction and the rigid polyester molded insert ensures that the part does not pull out of its retainer.
Splice & Notching Options
For extruded compression seals, gaskets, tubing, and bumpers, we offer a number of secondary processes, including butt splicing into one continuous loop, mitre splicing profiles into a 90 degree corner, molding and splicing radiused corners, notching corners, and finally notching and punching to allow for mechanical fastening.
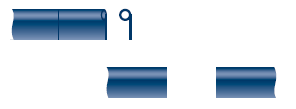
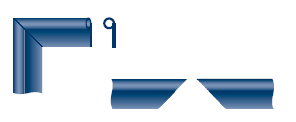
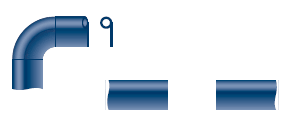
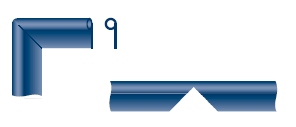
Notched Corners
Notched corners employ aspects of the mitre splice, but accomplish it without having to fully cut the extrusion. This method works particularly well with P-strip or J-seal design.