Our Innovation Process
Our Collaborative Innovation Process, Under One Roof
Our collaborative innovation process fuels innovation and shortens development times. By engaging with R&D engineers early in the development process, we’re able to create better components and significantly enhance the value of our customers’ products. Explore our immersive design-prototype-build-test process that can be uniquely executed under one roof in our new innovation center to get your differentiated product to market faster than ever.
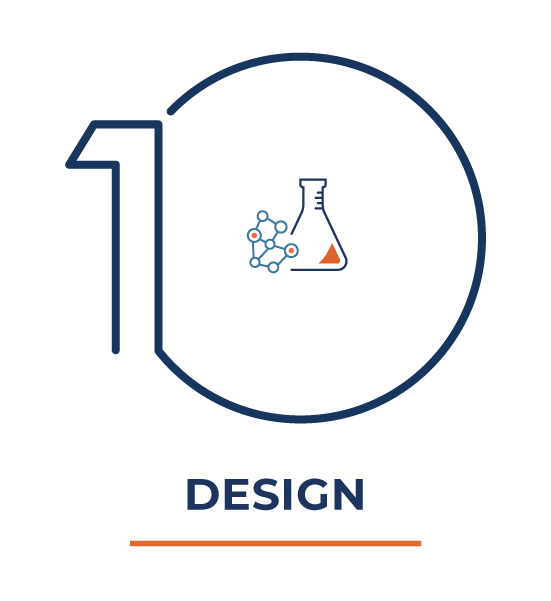
Designed for Manufacturability
With clients in high-regulation fields such as medical device manufacturing, we are accustomed to delivering critical-to-function components in accelerated timelines. We bring materials scientists, process engineers and tooling engineers together from day one — equipped with the right knowledge to ensure components are designed for scale-ready production from the beginning.
Custom Materials Formulations
Better performing devices are built with thoughtful designs and the right materials. We often see standard material formulations performing below expectations — and over-engineered designs attempting to compensate (and often failing). We provide extensive expertise in custom rubber formulations to meet demanding specifications.
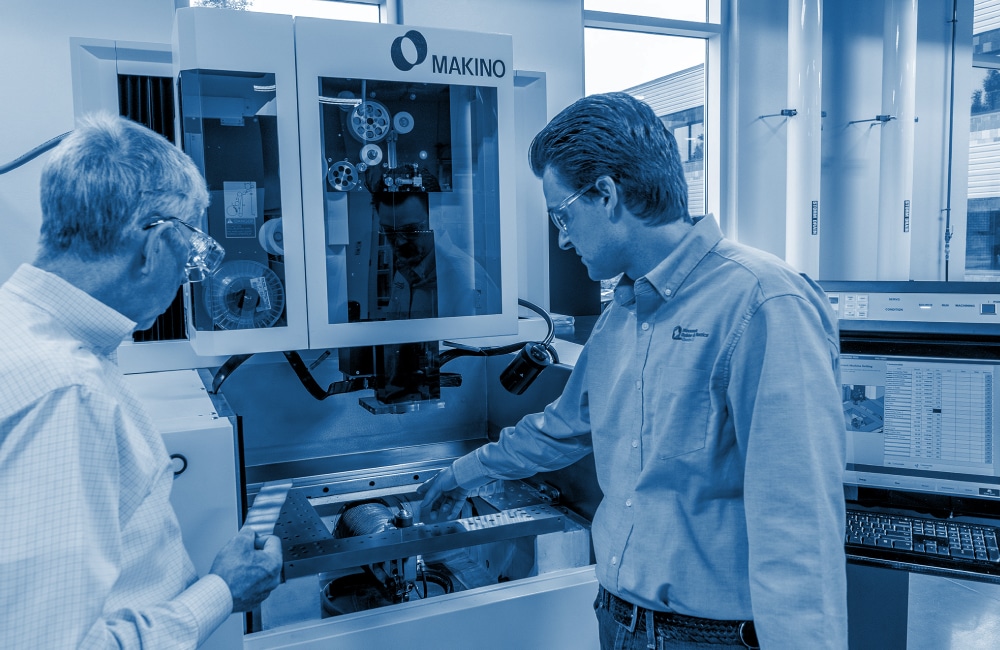
Production-intent Prototypes
Our ability to produce production-intent prototypes from any material in our ever-expanding library of custom rubber, silicone, and thermoplastics saves even more time, allowing our customers to test fully functional prototypes of critical-to-function components early in the innovation process. Product development cycles that once took months can now be accomplished in days.

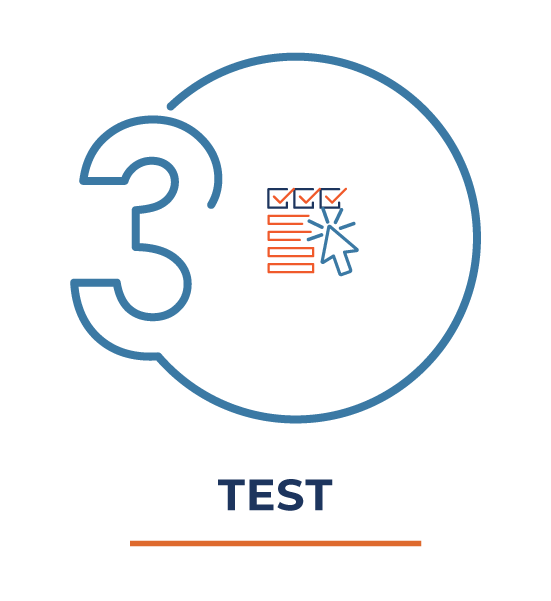
Comprehensive Testing
Product and material development testing covers a comprehensive range of services including contact-free laser and vision inspection, advanced failure analysis technology and simulated real-world testing to ensure full field confidence.
Additional Materials Testing Capabilities Include:
- Physical Property Testing
- Mechanical Property Testing
- Original and Aged Material Property Testing
- Rheological Testing
- Microscopy
- Chemical and Thermal Analysis
- Environmental Analysis
- General Pressurized Water Mechanical Testing
- Flow Control Testing
- Low Pressure/ Vacuum Testing
- Frictional/Torque Testing
- Heat Transfer Testing
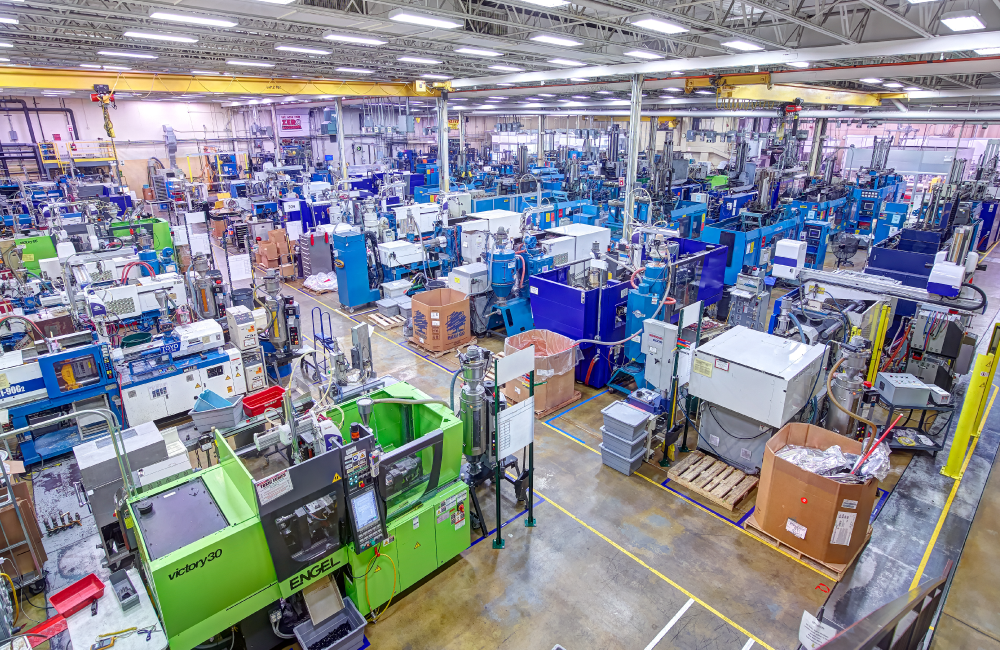
Manufacturing & Deployment
Whether you are manufacturing a component or a complex assembly, we provide in-house rubber, LSR, HCR, thermoplastic molding, insert molding and over-molding of dissimilar materials — all designed for production at scale.
We specialize in the assembly of close tolerance components and our assembly services include in-process and final testing, as well as 100% automated vision inspection for many medical applications in our ISO Class 7 and 8 clean rooms.
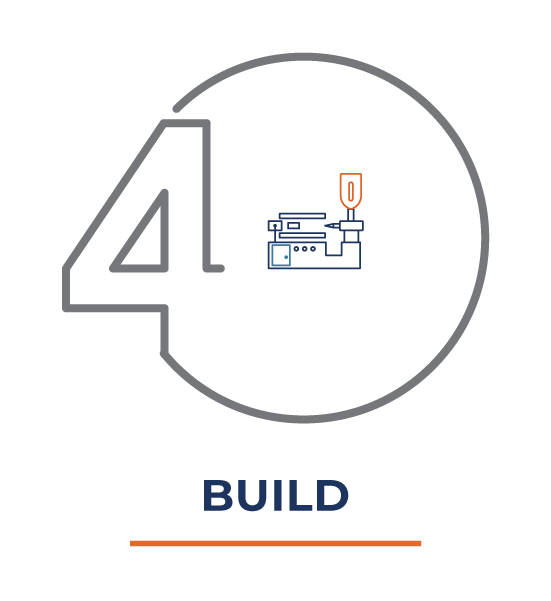