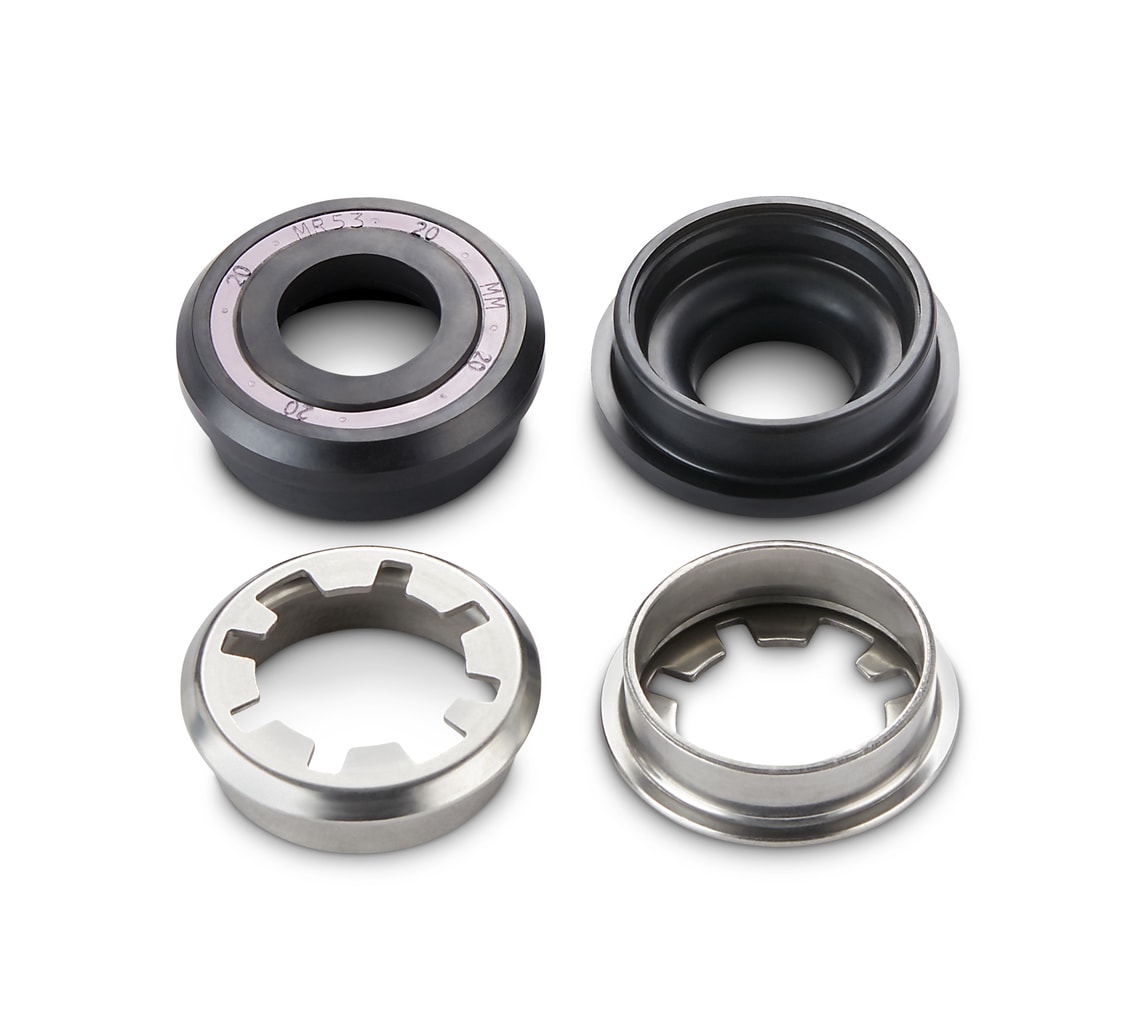
Applications
Our specialty materials and processes are developed and designed especially for medical and pharmaceutical manufacturing equipment. From low bleed, USP Class VI certified (see CVI series) and FDA-compliant materials, to unique inflatable seal designs, special cleaning procedures, and controlled (white room) manufacturing facilities, we are prepared to handle the unique requirements of the medical and pharmaceutical industries.
Inflatable Sterilizer Door Seals
Inflatable seals in durable fabric reinforced silicone or EPDM rubber profiles are ideal for:
- Sealing vertical lift doors on floor mounted sterilizers
- Sliding doors on table top models
- Large sliding doors on walk-in batch processing gas sterilizers.
Rectangular, Type 10X high-pressure profiles are frequently chosen for autoclave doors to minimize particle trapping pockets.
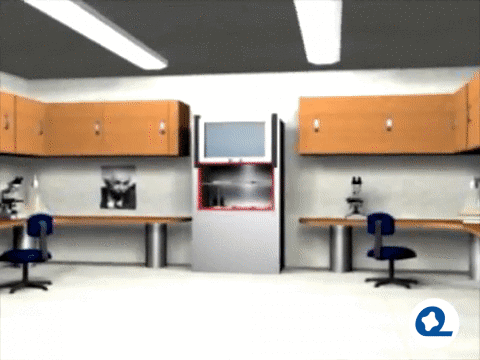
Glovebox Isolator Inflatable Door Seals
Glovebox isolation chambers are used in many different processes where maintaining a sterile working environment is critical to the success of the end product. To maintain the safety and quality of the final product, it is essential that the seals for these chambers are infallible. Optimal glovebox designs incorporate the use of pharmaceutical inflatable seals along the perimeter of a large plexiglass door, which allows for a high level of visibility and easy access to the chamber when necessary. Unlike a compression seal, which requires an elaborate flanging system, access to the chamber with an inflatable seal is as simple as deflating and lifting the door.
Our Inflatable Seals are perfectly suited for glovebox isolator doors. Our Type 1 (footed) or Type 10 (high pressure; low gap) inflatable seal profiles work very well in these rectangular, radial expansion outward applications. These profiles are also available in our new CVI™ series of USP Class VI compounds or in FDA-compliant white (or red) silicone.
Inflatable Door Seals for Tablet Coaters
Large tablet coating equipment relies on smooth batch-to-batch transfer along with ease of cleaning between runs. To ensure a productive and high-quality process the seals used for the equipment door opening must be reliable. Inflatable seals can be used to seal both the cleaning/inspecting access doors and drum entry openings. The use of inflatable seals allows operators access into the machine quickly for swabbing and routine inspection.
We can provide the optimal inflatable seal solution for your tablet coating equipment. Our Type 10X (high pressure; low gap) profiles prove easy to clean and, with a robust cross-sectional wall, promote long life. These profiles are readily available in our new CVI™ series of USP Class VI compounds or in FDA-compliant white (or red) silicone.

A new line of inflatable seals which meet US Pharmacopoeia (USP) Class VI certification is now available. The CVI™ Series meets the specific needs of pharmaceutical equipment manufacturers who seek the assurance of USP Class VI compound certification for their inflatable seals.
The CVI Series combines use of the right materials for biocompatibility with the unique characteristics needed for inflatable seals, including temperature and/or chemical resistance. These compounds address a growing trend among pharmaceutical equipment manufacturers towards use of materials that are certified to USP Class VI, the most stringent protocol for classification of compounds used in most medical and other healthcare applications. Among many advantages certification offers is an added level of confidence that assures favorable compatibility results, reducing the burden of regulatory compliance.