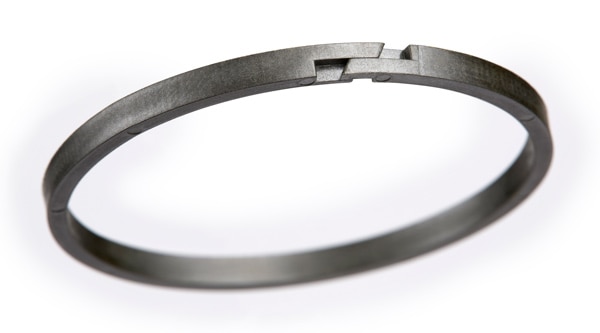
Applications
Minnesota Rubber & Plastics has been an automotive seal ring supplier to numerous OEMs for over 25 years. Annually, we produce 20 million seal rings for ePowertrain, CVT and clutch applications.
Modern ePowertrain systems rely on high-performance thermoplastic seal rings to maintain pressure and keep precision parts lubricated while working flawlessly. Sealing failures can turn expensive systems into scrap metal.
Benefits
What are thermoplastic seal rings?
Modern ePowertrain systems are costly to develop and test. Internal components rotate at high speeds and generate high friction.
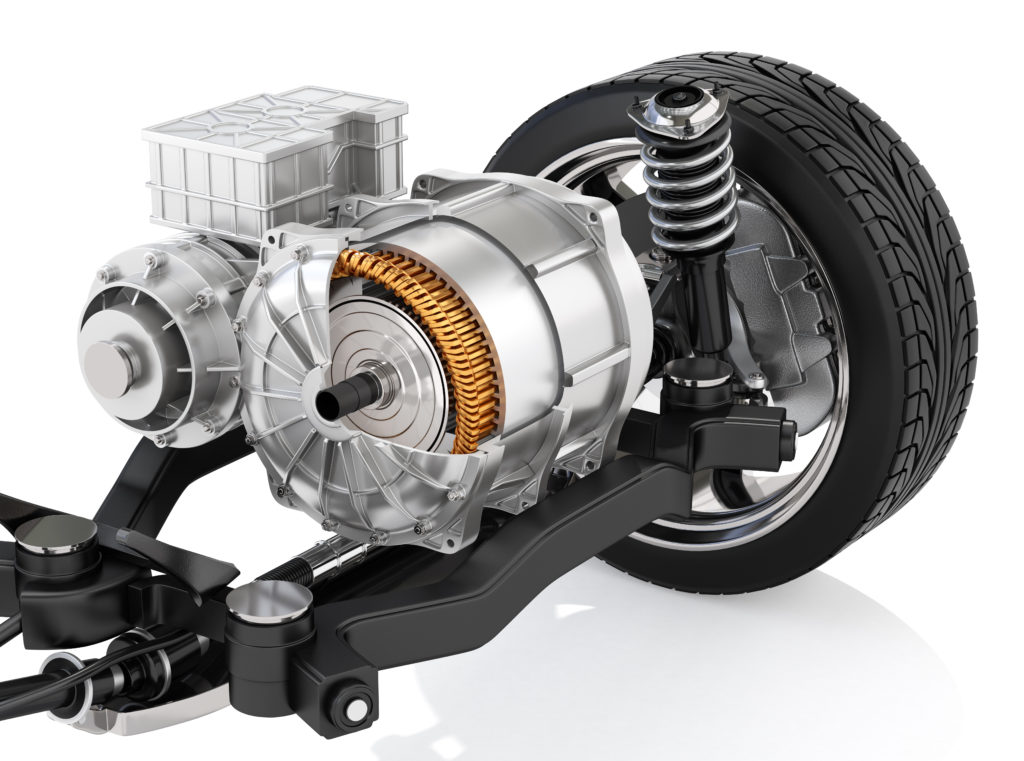
The seal rings must have expertly engineered geometry to meet OEM target leakage rates, pressure, temperature and speed specifications. These critical components are essential in allowing the device to shift smoothly—and optimize mechanical/friction efficiencies. In a torque management application, the seals ensure precise hydraulic actuation. (The tighter the seal, the more accurate hydraulic control.)
Design engineers turn to Minnesota Rubber & Plastics to help them design, test and manufacture these precision-molded plastic seal rings.
Material science: Ensuring our thermoplastic seal rings perform under variable temperatures
Through extensive research within our advanced materials lab, we ensure our thermoplastic seal rings are optimized for the heat and pressures generated by ePowertrain systems. We study the relationship between material structure, its properties, how processing affects characteristics, and how the materials perform in an application.
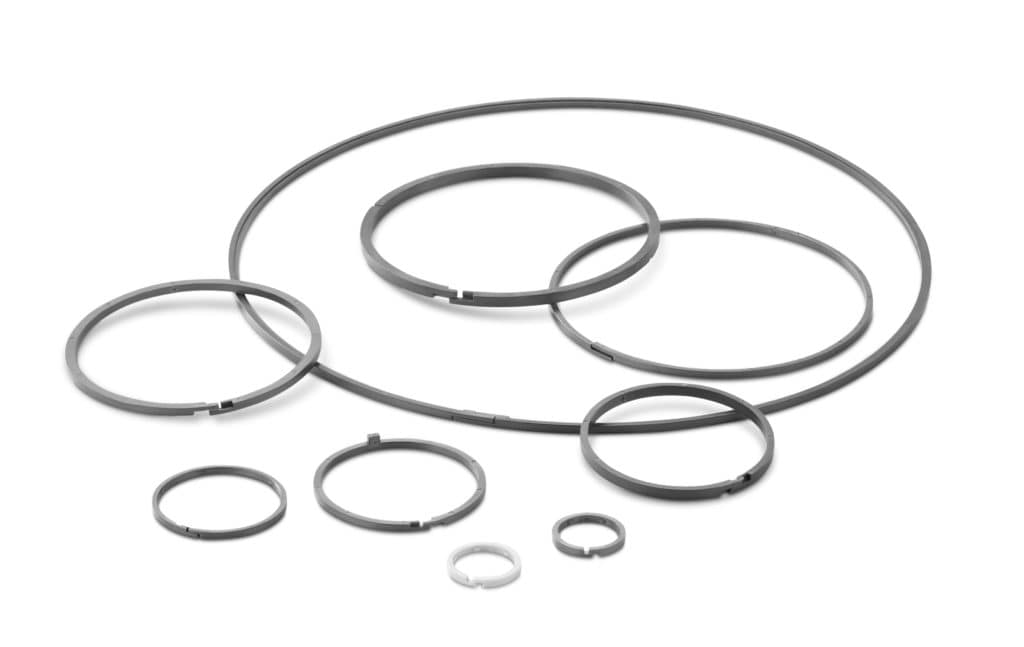
Molding and manufacturing: Creating the perfect seal
Engineers must analyze and optimize the injection molding steps needed to build a perfect seal ring before mass production. This step is essential to optimize gate location, ensure cavities are filled uniformly, evaluate various materials, and to identify potential visual defects. For these reasons, more engineers turn to us for our superior capabilities with tight-tolerance dimensions.
A scientific approach to molding is critical for developing optimum control of the injection molding process, which includes constant monitoring of cavity pressures. Tooling is also important because part quality directly impacts sealing performance.