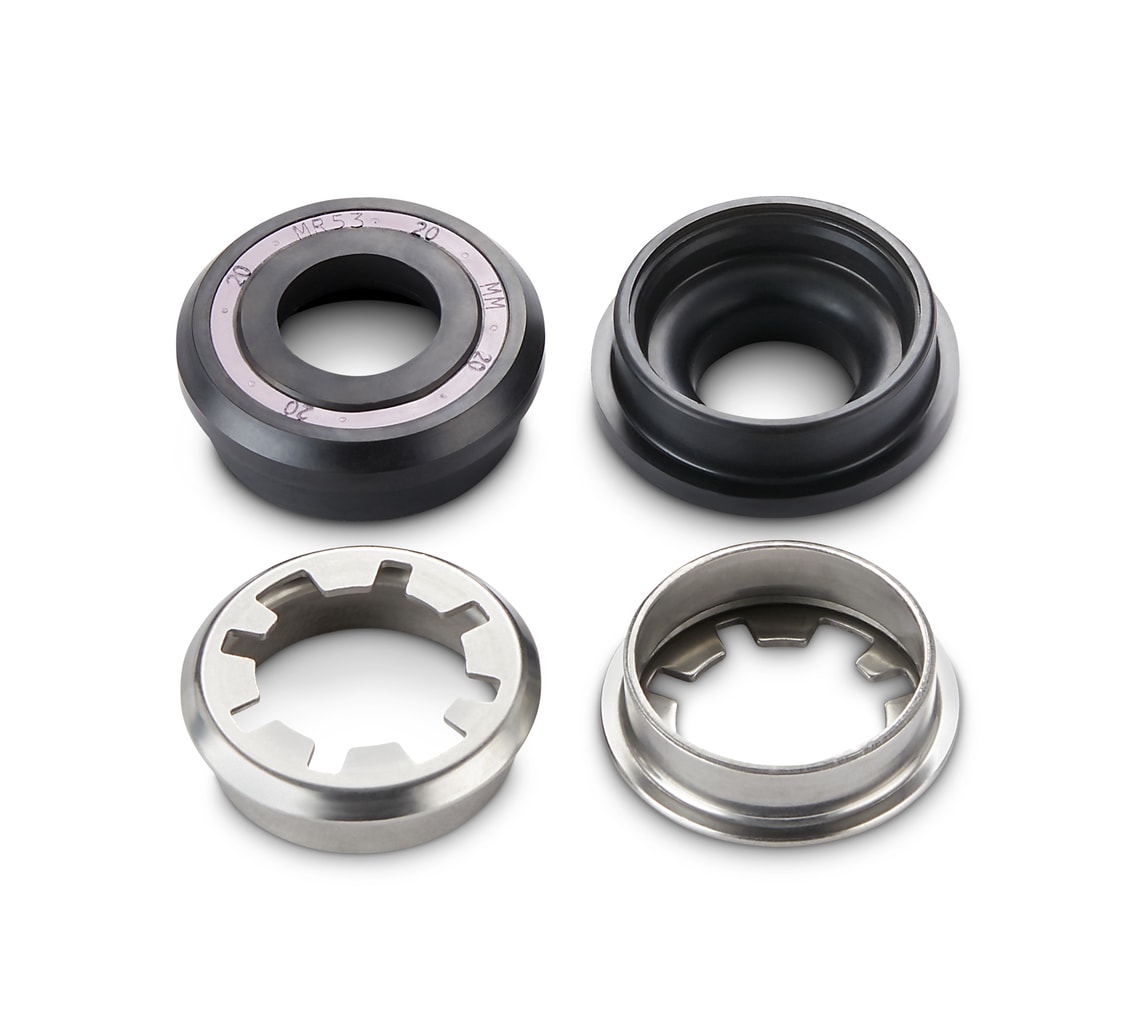
Trelleborg Food and Beverage Applications
The expertise to provide the optimum seal.
The strength of Trelleborg Sealing Solutions has always been our deep application knowledge of the food and beverage industry. Many thousands of successful customer projects, using both standard products and engineered solutions, have made us the technology leading company in these sectors.
Application examples for the Food & Beverage industry
- Helping maximize production in systems fitted with mix proof valves
- Optimum sealing material for flange gaskets
- Superior chemical resistance in quick couplings
- Bonded part gives advantages in safety valves
- Turcon® Variseal® Hi-Clean eliminates contamination in filling machines
- Seal configuration used in unique retractable tank spray system
- Modified Stepseal® in Turcon® MF helps coffee machine maker
- FlexiMold™ O-Ring seals centrifuge housing

FlexiMold™ O-Ring seals centrifuge housing
A centrifuge manufacturer specializing in the pharmaceutical industry needed large size O-Rings for the housing of one of their products.
Sealing issue:
The seals are exposed to high centrifugal forces, which put extreme demand on the physical properties of the seals. Additionally the seals needed to fit in the seal groove without creating dead space, so the centrifuge could be cleaned easily.
Sealing requirements:
- Compatible with harsh cleaning medias such as a variety of solvents
- Compliant with FDA and USP Class VI standards
Solution:
Due to the low volume requirement, the cost for a tool was prohibitive. An O-Ring using the FlexiMold™ process was therefore selected. By this proprietary production method, an O-Ring can be fabricated that has the same characteristics, including integrity at the join, as a molded O-Ring without the need for a dedicated tool. To ensure compatibility with process media, Isolast® J9515 was specified.
Result:
The giant O-Rings were delivered in record time providing the same integrity as compression molded O-Rings without the tooling cost.

Coffee machine
Modified Stepseal® in Turcon® MF helps coffee machine maker
Professional coffee machines need to brew up to 300 cups of coffee per hour. This puts high demands on all components, especially their seals.
Sealing issue:
In professional coffee machines, components are metal, as opposed to the plastic of the domestic models.
Harder surfaces combined with abrasive coffee beans mean that seals tend to wear quickly. A leading professional coffee machine producer worked with Trelleborg Sealing Solutions to maximize seal life with a target of 100,000 cycles before maintenance.
Sealing requirements:
- Cope with wear from abrasive coffee beans
- Compatible with fat and acids in process media
- Operate at a pressure of 16-bar/2320 psi in hot water
- Withstand CIP media
- FDA compliant
Solution:
To achieve the abrasion resistance the customer requested, the Turcon® Stepseal® surface was modified. Additionally a FDA compliant MF grade material was selected which was compatible with process the media, could withstand cleaning regimes and operate at high pressure.
Result:
In tests, the modified Turcon® Stepseal® design achieved the required cycles and is now fitted in a number of coffee machine models.
More information on Turcon® MF
Find out about Turcon® Stepseal® 2K
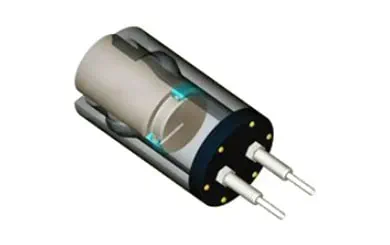
Filling machines
Turcon® Variseal® Hi-Clean eliminates contamination in filling machines
Filling machines have numerous filling heads activated by pistons.
Sealing issue:
A filling machine manufacturer discovered fruit particles were being trapped in elastomer seals used within their filling heads. This led to contamination, which was difficult to clean out due to seal design. In addition, the elastomers were sticking to the piston shaft, impeding piston motion and making filling erratic.
Sealing requirements:
- High chemical resistance
- Withstand CIP chemicals and operate in steam up to 150°C / 302°F
- Compliant with FDA and USP Class VI standards
Solution:
Trelleborg Sealing Solutions recommended replacing the elastomer seal with a Turcon® Variseal® Hi-Clean. As it fitted into the existing O-Ring groove, no equipment redesign was necessary. The stainless steel spring that energizes the seal is encased in silicone. This means that it is easily cleaned and sterilized with no risk of contamination. The low friction characteristics of the Turcon® PTFE based material prevents sticking, even after extended periods of rest. The grade of Turcon® MF material chosen was also compliant to all relevant approvals.
Result:
In application, the Turcon® Variseal® Hi-Clean eliminated all risk of contamination. In addition filling action was improved due to the low friction characteristics of the seal.
More information on Turcon® MF
Find out about Turcon® Variseal® Hi-Clean
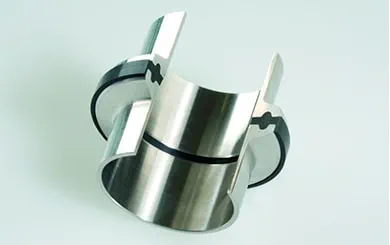
Flange gaskets
Optimum sealing material for flange gaskets
In today’s processing plants, there are thousands of lengths of piping and at each juncture, a coupling. These are sealed with clamp gaskets and O-Rings. Though the individual cost of these may be relatively insignificant, their cost in terms of maintenance can be extremely high.
Sealing issue:
Constantly in contact with system media and subject to aggressive cleaning regimes, flange gaskets used to seal pipe work connections within a processing system of a global pharmaceutical company deteriorated quickly. Our customer wanted to reduce maintenance costs by extending intervals between planned maintenance cost-effectively. However, sealing integrity could not be compromised, as any contamination involved a major cost in scrapping production batches.
Sealing requirements:
- Withstand mixture of alkaline and acidic CIP medias
- Compliant with FDA, USP Class VI and 3-A standards
- Long seal life to extend intervals between planned maintenance
Solution:
Trelleborg Sealing Solutions has undertaken a number of tests to determine the optimum material for use in CIP chemicals. Based upon these results, it was recommended that the flange gaskets were replaced by ones manufactured in a specific EPDM compound.
Result:
The change in material for the flange gaskets proved to extend seal life and achieved the objective of increased productivity, extending meantime between planned maintenance. In addition, as the EPDM compound was specifically engineered for aseptic applications, contamination was reduced.
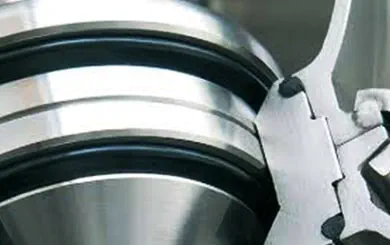
Mix proof valves
Helping maximize production in systems fitted with mix proof valves
Mix proof valves are key components in automated matrix-piped processing plants. The plants can be used for the production of all sorts of products, ranging from food and beverage to pharmaceuticals and cosmetics. The mix proof valves allow for concurrent processing and cleaning of the system, while at the same time prevent mixing of media.
Sealing issue:
Trelleborg Sealing Solutions was contacted by a leading international valve manufacturer to help develop the sealing configuration for the new generation of valves. Since the valves were required to be in operation 24 hours per day, the seals come under attack both from high concentration CIP media and super heated steam. Additionally, several of the seals were used dynamically.
Sealing requirements:
- All sealing materials need to comply with FDA standards
- Have good chemical resistance to oil and fat, ozone and aging
- Allow for a thermal range up to 200°C / 392°F
- Withstand cleaning fluids at a concentration up to 5% acids at 100°C / 212°F and 5% bases at 40°C / 104°F
- Withstand sterilization in steam
Solution:
Trelleborg Sealing Solutions worked with the valve manufacturer from initial development of the product. By using FEA (Finite Element Analysis) and 3D modeling we identified the best geometry for an engineered seal to maximize sealing integrity. A FKM compound was selected due to its chemical compatibility to production media as well as cleaning regimes and steam.
Result:
The recommended sealing configuration has been fitted in volume to valves in a variety of liquid handling situations. They are proving to withstand CIP and SIP regimes, lengthening intervals between planned maintenance and maximizing production yield.
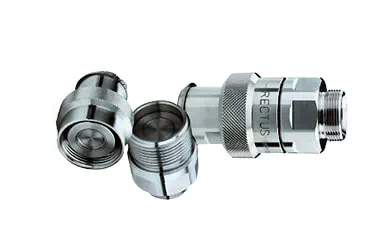
Quick couplings
Superior chemical resistance in quick couplings
Quick couplings are now extensively used in process lines to allow for a flexible production system and to make maintenance and repair quicker and easier.
Sealing issue:
A leading quick coupling manufacturer wanted to develop a coupling for use in the chemical and beverage industry. The elastomer seals that they usually fitted in their product would not stand up to the harsh conditions of these processing lines. They approached Trelleborg Sealing Solutions for a solution that would be chemical and steam resistant while complying with relevant industry standards.
Sealing requirements:
- High chemical resistance
- Withstand CIP chemicals and operate in superheated steam.
- Compliant with FDA and USP Class VI standards
- Tight tolerances
Solution:
Depending on cleaning regimes and process media, Trelleborg Sealing Solutions recommended O-Rings in either EPDM or Isolast®.
Result:
By using seals in these materials, quick couplings could be effectively cleaned and sterilized without causing deterioration of the O-Rings. This meant that the customers of the coupling manufacturer benefited from long component life.
Find out about Isolast®
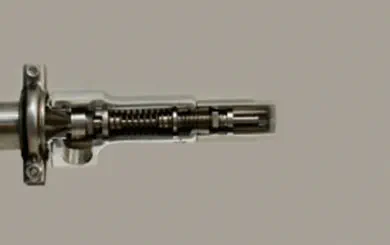
Safety valves
Bonded part gives advantages in safety valves
Safety valves are installed to protect critical equipment.
Sealing issue:
A major medical equipment manufacturer had an existing design of safety valve. The seal was contained within a three-piece assembly. The manufacturer wanted to increase the chemical resistance of the sealing element by specifying a FFKM material. Trelleborg Sealing Solutions believed by value engineering the complete assembly they could offer the customer a cost-effective sealing component that would improve integrity.
Sealing requirements:
- High chemical resistance
- Withstand CIP chemicals and operate in steam up to 150°C / 302°F
- Compliant with FDA and USP Class VI standards
Solution:
With unique bonding technology, we were able to bond our Isolast® material to metal. This allowed the three separate components of the assembly to be produced as one item.
Result:
The resulting design of sealing element proved to be highly cost effective. Total cost was reduced by extending replacement intervals, a reduction in the amount of sealing material required and lower assembly costs. The component proved highly effective and the same concept is being used across their product range.
Find out about Isolast®
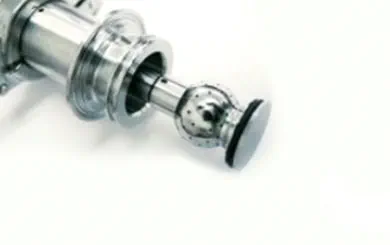
Tank spray systems
Seal configuration used in unique retractable tank spray system
Spraying systems are incorporated into tanks to clean them. Generally the spray head is now retracted automatically from the tank.
Sealing issue:
Trelleborg Sealing Solutions worked with a manufacturer who was developing a unique retractable spray ball system. It operates pneumatically which allows it to have the major benefit of being self-draining. A complete sealing configuration was required which could operate with liquid on the one side and air on the other. Under pressure from both sides and at high temperature, seals in contact with cleaning media had to withstand the harsh chemicals used in these regimes.
Sealing requirements:
- High chemical resistance
- Chemically resistant to all types of CIP media
- Compliant with FDA and USP Class VI standards
Solution:
Trelleborg Sealing Solutions recommended a configuration of seals including a Turcon® Variseal®, along with O-Rings in EPDM and Isolast® options depending on chemical resistance requirement. The surface of the elastomer O-Ring at the neck of the spray ball was treated with FDA compliant FF coating. This gave the seal the necessary friction characteristics to allow smooth dynamic operation of the spray head.
Result:
The seal configuration withstood extensive tests. After cycles of 1,000 operations, there was no leakage and pressure was held. The seals also continued to perform after a temperature test where the units were heated up to 140°C / 284°F for 24 hours.