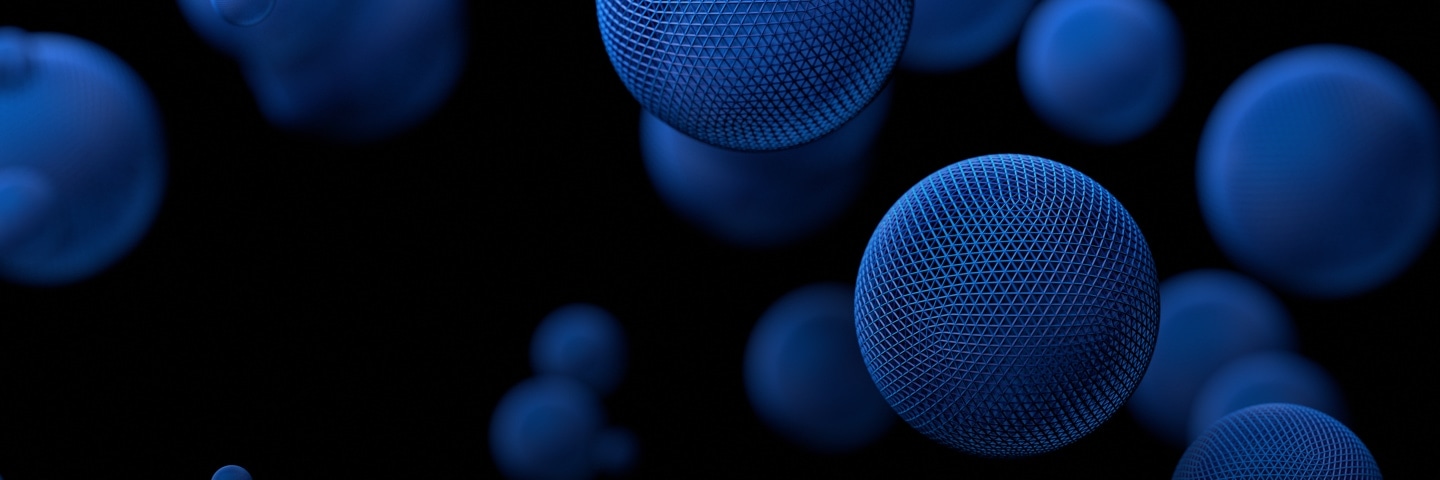
Case Study
Custom Formulated Material Delivers High Performance for a Surgical Seal Solution
Challenge
A large medical technology company aimed to upgrade its medical device solution used primarily to cut and cauterize tissue in minimally invasive surgeries. The goal was to improve the design to allow surgeons to reuse the device by creating a disposable biocompatible flexible sleeve cover for the surgical instrument. If the concept succeeded, the solution’s value proposition for surgeons would increase by improving clinical outcomes and lowering total cost of ownership.
To achieve success, the new boot needed to meet several critical feature and function factors, including: be thin (0.55mm), flexible and biocompatible, resist tearing and heat, reduce coefficient friction, provide ease of installation and removal, and maintain physician mobility and the integrity of the protective barrier.
Initially, the company had worked with other suppliers that missed the materials mark. In these cases, the silicone compound used lacked consistency and durability, which jeopardized the effectiveness and integrity of the surgical procedure and clinical outcomes.
Solution
Understanding the inherent challenge of developing a custom material for this critical component, MRP’s product engineers and material science chemists collaborated closely with the company’s technical team.
The MR&P team began by optimizing the chemical properties based on the known variables and requirements for the component. To meet the heat resistance need, the team selected fluoroelastomer (FKM). To augment the difficulty of creating the thin cross section part from FKM, the team developed two materials with three hardness ranges for the customer evaluation and performance analysis testing. The key characteristic of the material addressed the high temperature performance, as the tip of the device experienced elevated temperatures during use. Variations in the material modulus across the two material sets provided a range of resistance options for the physician to evaluate tactile feel. A surface coating was added to address the low friction requirement for ease of installation to the instrument.
Results
In the end, nine sample configurations were evaluated and adjusted to deliver the final high-performance sealing solution. In fact, the custom-formulated compound delivered a 277% increase in tear strength and 287% increase in elongation, demonstrating significantly improved resilience.
Both teams were extremely pleased with the specialty compound solution — and the collaborative process that led to meeting the product’s performance needs. Based on the success of this project, the company selected MRP to carry the product forward through prototyping and production.
Original properties | C2525LG (FKM) | General-purpose silicone |
---|---|---|
Hardness (ASTM D 2240), Shore A | 76 | 81 |
Tensile Strength (ASTM D 412), MPa (psi) | 17.0 (2,462) | 8.2 (1,186) |
Elongation (ASTM D 412), % | 359 | 125 |
Modulus @ 100% Elong (ASTM D 412), MPa (psi) | 5.7 (826) | 7.0 (1,010) |
Tear Strength | 21.9 (125) | 7.9 (45) |
Color | Gray | Red |
Print-Ready Case Study
Download this surgical seal case study in PDF format.
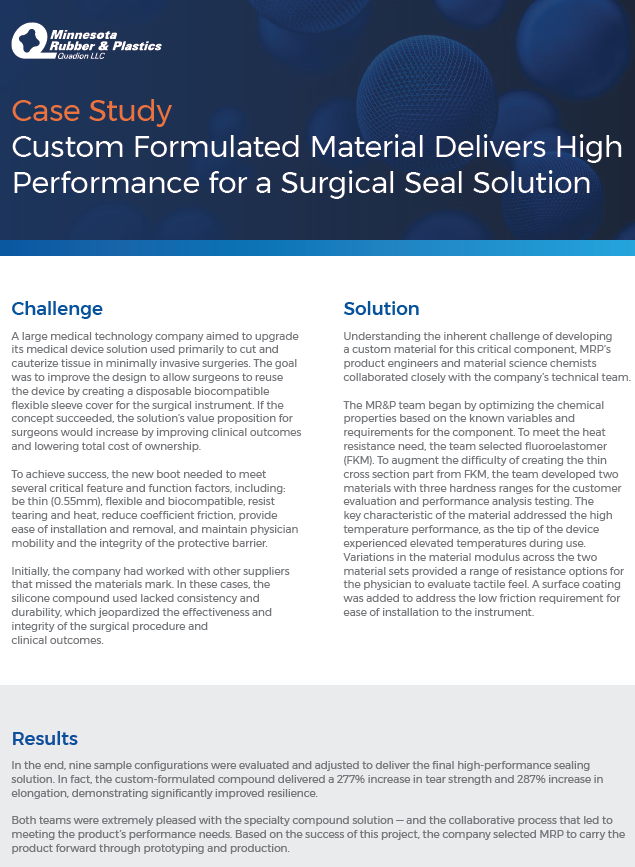