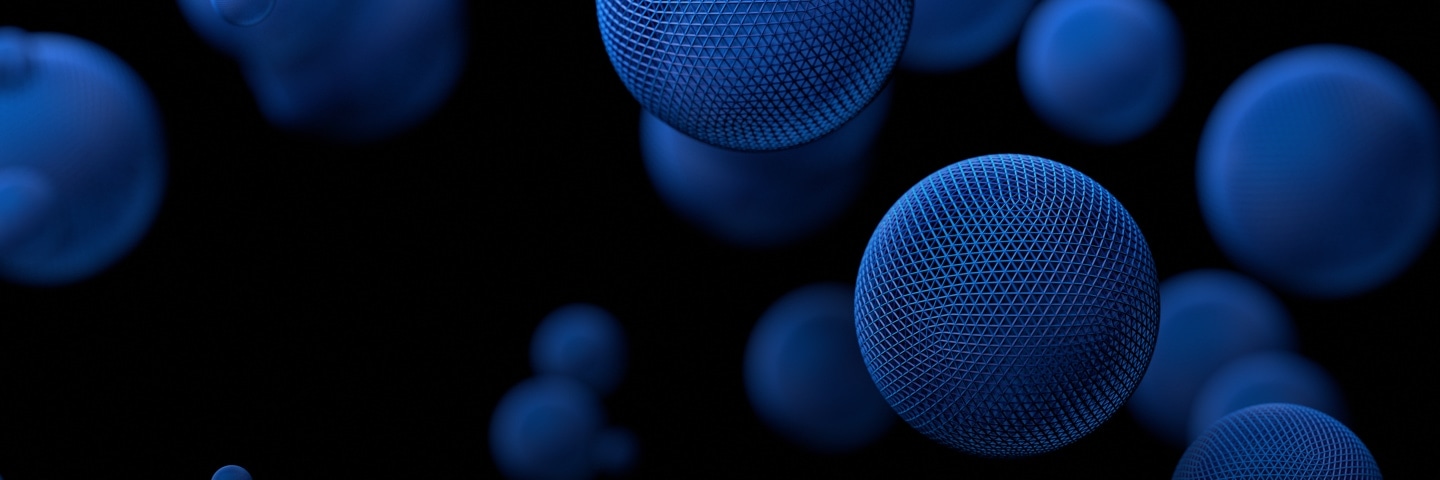
Case Study
A New Material and Design for Rubber Umbrella and Bell Valves with Excellent Elongation at Break
Challenge
Redesign and manufacture rubber umbrella and bell valves to operate longer without breaking and improve sealing performance.
Our client wanted us to create a custom rubber material for umbrella and bell valves leading to a more robust version of existing critical pump sealing components. At the same time, we would develop the material and manufacture the valves from our design facility in China, close to our client’s manufacturing operations.
The client was eager to have an alternate supplier located in Southern China in addition to its current local supplier. The new compound is an ideal candidate to manufacture using highly efficient vertical injection processes.
We also needed to improve the umbrella valve’s sealing performance, which would require a refined design and a new molding concept.
Solution
Created a new advanced material and part design that significantly improves elongation at break performance.
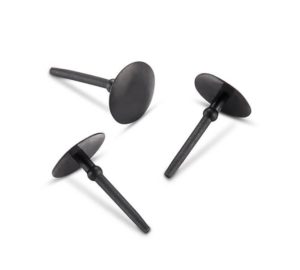
Since our customer had manufacturing facilities near our China operations, we tapped our nearby advanced materials group to create the valves’ new elastomer compound. Additionally, this led the redesign of the part to improve sealing performance by enhancing surface topography.
Our tooling engineers improved demolding efficiency and reduced production costs. The new material also had to be more robust than previous parts.
Production molds for both the bell and umbrella valves were made up of several small groups, making it easy to replace molds and reduce mold costs. For high-volume part runs, low-cost replacement molds help to scale production efficiently and economically.
Finally, this increases mold accuracy and provides a stable parts supply because of the small part size.
Results
Better valve sealing performance; elongation at break achieves 662%.
To meet the customer’s requirements to improve the umbrella valve’s sealing performance, MRP developed a processing technology to achieve surface topography that enhances sealing performance. Additionally, the mold design improved pump performance by increasing the umbrella valve’s ability to seal onto the mating surface. Even the smallest efficiency gains with these valves have a substantial impact on overall pump performance. Elongation at break tests would later confirm the new material achieves 662% elongation, a critical improvement. Having the ability to develop and manufacture our customer’s parts in China was critical for them as they expand their footprint in this part of the world. This proximity improved efficiencies, took less time and lowered costs.
Print-Ready Case Study
Download this case study in PDF format.
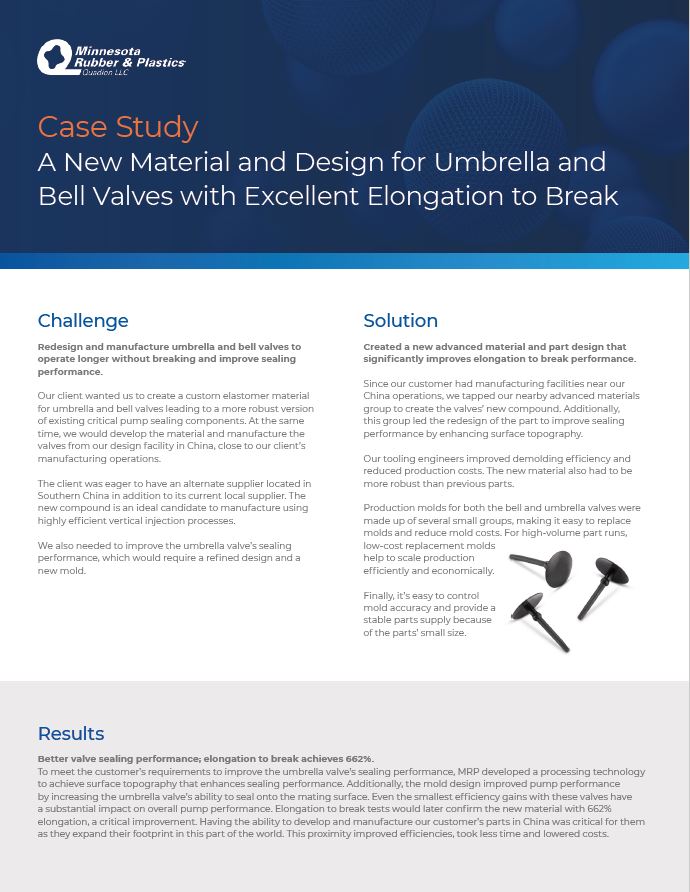