Custom Liquid Silicone Rubber (LSR) Injection Molding and Prototyping
Custom LSR design, prototyping and manufacturing company for complex components in medical devices, water food & beverage and other demanding industries.
Turnkey LSR capabilities-design, Prototyping, Tooling and Injection Molding Manufacturing Company
If you’re looking for a proven design to injection molding manufacturing resource for your custom LSR projects, our company has you covered. LSR is among a large portfolio of elastomers our customers spec for projects requiring unique properties. For example, in medical device applications LSR is a common material choice because of its biocompatibility with body tissue.
Experts within our advanced materials lab can help you make the right materials choices. Our materials scientists are experts in the full range of platinum cured silicones and peroxide cured silicones. One of our materials scientists will help you determine if the on-spec requirements are the best choice for the application, or if an alternative off-spec material choice will provide a higher level of quality, reliability and performance to the end product.
From designing, prototyping, tooling management, manufacturing, and distribution, we comply with all regulatory guidelines, including ISO 13485 and 21CFR820.
For years, engineers have relied on LSR for high volume applications where the parts leave the line in a ready-to-ship state, which often positively impacts quality and cost. Because parts can be produced with minimal waste, LSR is an excellent elastomer option. The material is also ideal for applications requiring extreme low and high temperatures, and it provides excellent fluid compatibility across a broad range of environments.
Our LSR customers include fortune 500, Inc. 5000 through startup companies
We have LSR customers in a multitude of demanding markets across a broad range of company sizes. As always, your engineering team will have quick and easy access to our technical teams to make sure your LSR project runs smoothly. Customers that prototype with us gain access to our new state of the art innovation center that produces production-intent prototypes at unparalleled speed. With our innovation center, prototype projects that used to take months can now be accomplished in days.
Turn to us to help you compound, mix, design and manufacture hard-to-build custom LSR parts. Whether it’s a turnkey multi-shot part with million-dollar tooling, a complex overmold, or a system-critical part for a wearable diabetes application, we have the resources and deep bench of expertise to deliver your toughest projects.
Minnesota Rubber and Plastics now is a part of Trelleborg, a global leader in LSR in healthcare and industrial applications. Learn More >
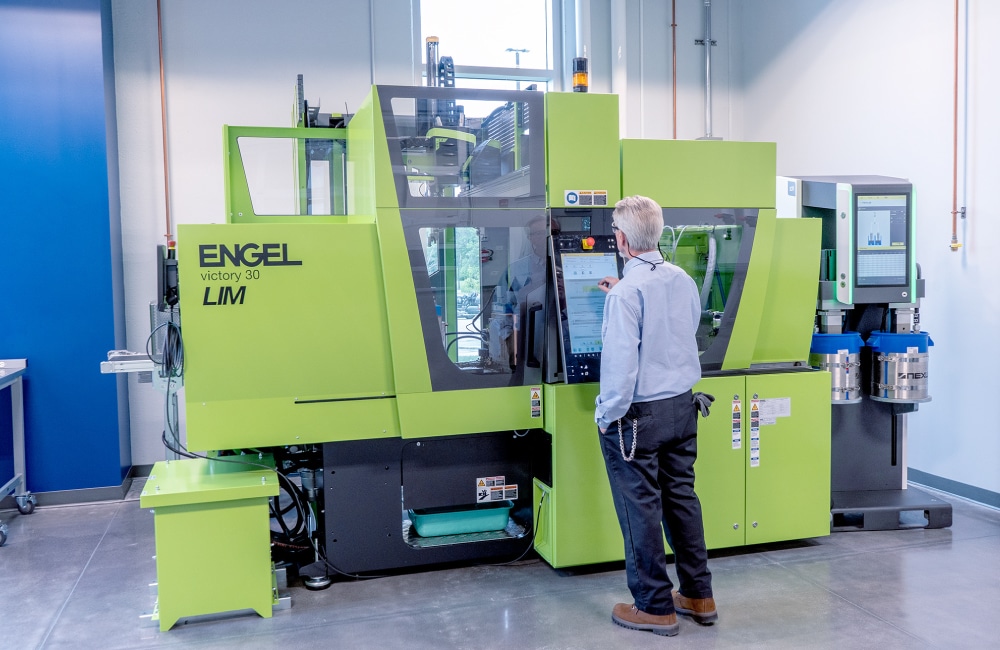
Designing and Creating LSR Prototypes with Manufacturing in Mind
Some customers call us after they discover the prototype they contracted to build was delivered with a minor flaw: unfortunately it couldn’t be manufactured. You’d be surprised how often that happens; in the haste to build a quick prototype, designers/engineers with limited elastomer experience end up with a seemingly perfect design, yet it’s impossible to manufacture at scale.
We collaborate with you early in the project to focus on quality and better understand the design input and output requirements of your custom parts. Allowing us to better understand the design intent of the product, will lead to a smoother product launch, greatly reducing future risk. Examples of questions we will help you answer include:
We’ll Help You Avoid and Mitigate Significant Risks in LSR Projects
We’ll collaborate with you early in a project to help you consider quality and certifications to avoid rework that increases cost and delays projects. Rely on us to:
The more we work together and share information the more our experts can help anticipate your needs and avoid and mitigate risks to your project.
Design Engineers: Read our Design Guide
We wrote this for design engineers because you don’t have time to become a rubber or plastics expert. That’s our job.
To gain a better understanding of the processes, materials and technical considerations involved in the design and manufacture of custom-molded rubber, read through our Engineer Design Guide. This comprehensive design tool details both rubber and plastic design issues including a materials overview and prototype mold design considerations.