Minnesota Rubber and Plastics announced that it has doubled its clean room manufacturing capacity at its Litchfield, Minnesota facilities. The expansion is in response to rapid growth of the company’s medical device business.
As a leading molder of high performance elastomers and thermoplastics to the medical device industry, Minnesota Rubber and Plastics added a new Class 8 clean room at its 70,000 sqft Litchfield manufacturing facility.
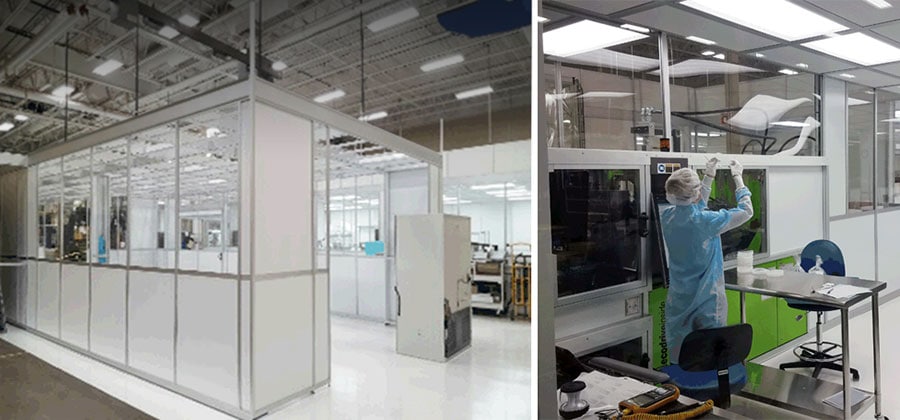
The Litchfield operations are highly automated that include horizontal injection and vertical compression/transfer presses for processing high performance elastomers and liquid silicone rubber. Significant medical processing capabilities include contaminant-free white room and clean room molding, finishing and assembly of complex medical device components and assemblies.
Litchfield’s expanded clean room facilities have been augmented with dozens of support systems, equipment and machines integrated into the enhanced manufacturing operations including the addition of new cleaning and packaging equipment.
Inspiring this growth is Minnesota Rubber and Plastics long-term orientation to science-based processes and procedures. These combined with leading edge technologies have fostered continued advances in material sciences, new product development launches and production standards. The company has developed a concerted program to implement continuous improvement of systems and procedures, with these new medical facilities in support of customer product performance goals.